Welding method for sputtering target material
A sputtering target material and welding method technology, which is applied in welding equipment, non-electric welding equipment, metal processing equipment, etc., can solve the problems of high cost of sputtering target material and restrictions on the development of chip manufacturing, so as to reduce costs and ensure success rate , High welding effect
- Summary
- Abstract
- Description
- Claims
- Application Information
AI Technical Summary
Problems solved by technology
Method used
Image
Examples
Embodiment 1
[0017] Embodiment 1: A sputtering target welding method provided by the present invention comprises the following steps:
[0018] (1) Adjust the welding gap between the main material and the auxiliary material of the sputtering target to 0.3mm;
[0019] (2) Welding with a friction stir welding machine: insert the rotary cutter on the friction stir welding machine into the welding gap to a depth of 10.5 mm, and rotate the rotary cutter for welding. During the rotary welding of the rotary cutter, the auxiliary material rotates with the main material.
[0020] Compared with any welding method of the prior art, the welding method of the present invention has an average welding success rate of 98%, while the average success rate of the prior art welding method is 40%. Good welds together form the sputtering target.
Embodiment 2
[0021] Embodiment 2: A sputtering target welding method provided by the present invention comprises the following steps:
[0022] (1) Adjust the welding gap between the main material and the auxiliary material of the sputtering target to 0.2mm;
[0023] (2) Welding with a friction stir welding machine: Insert the rotary cutter on the friction stir welding machine into the welding gap to a depth of 11mm, and the rotary cutter rotates for welding. During the rotary welding of the rotary cutter, the auxiliary material rotates with the main material.
[0024] Preferably, the auxiliary sputtering target material is aluminum. The rotation speed of the rotary cutter in the step (2) is 1400 rpm. The speed at which the main material rotates in the step (2) is 115mm / min. The soldering temperature is 617°C.
[0025] Adopting aluminum material to replace the materials in the prior art of auxiliary materials can greatly reduce the cost of raw materials. Compared with any welding method ...
Embodiment 3
[0026] Embodiment 3: A sputtering target welding method provided by the present invention comprises the following steps:
[0027] (1) Adjust the welding gap between the main material and the auxiliary material of the sputtering target to 0.1mm;
[0028] (2) Welding with a friction stir welding machine: Insert the rotary cutter on the friction stir welding machine into the welding gap to a depth of 10.6mm, and the rotary cutter rotates for welding. During the rotary welding of the rotary cutter, the auxiliary material rotates with the main material.
[0029] Preferably, the auxiliary sputtering target material is aluminum. The rotation speed of the rotary cutter in the step (2) is 1450 rpm. The speed at which the main material rotates in the step (2) is 120mm / min. The soldering temperature is 644°C.
[0030] Adopting aluminum material to replace the materials in the prior art of auxiliary materials can greatly reduce the cost of raw materials. Compared with any welding metho...
PUM
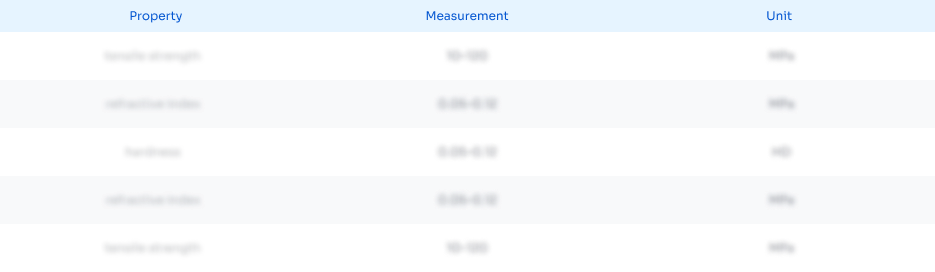
Abstract
Description
Claims
Application Information

- Generate Ideas
- Intellectual Property
- Life Sciences
- Materials
- Tech Scout
- Unparalleled Data Quality
- Higher Quality Content
- 60% Fewer Hallucinations
Browse by: Latest US Patents, China's latest patents, Technical Efficacy Thesaurus, Application Domain, Technology Topic, Popular Technical Reports.
© 2025 PatSnap. All rights reserved.Legal|Privacy policy|Modern Slavery Act Transparency Statement|Sitemap|About US| Contact US: help@patsnap.com