Radiation-proof thermal insulation concrete and preparation method thereof
A thermal insulation concrete and anti-radiation technology, which is applied in the field of building materials, can solve the problems of poor concrete construction performance, impact on radiation resistance performance, and poor anti-segregation performance, so as to improve workability, enhance electromagnetic wave absorption effect, and increase contact area effect
- Summary
- Abstract
- Description
- Claims
- Application Information
AI Technical Summary
Problems solved by technology
Method used
Image
Examples
Embodiment 1
[0024] Porous Flower Fe 3 O 4 Preparation: add anhydrous ferric chloride and urea to the ethylene glycol solution at a ratio of 1:10, stir and mix to obtain a mixed solution, transfer the mixed solution into the reactor, react at 230°C for 2h, and take it out after cooling , Filter, wash, and dry to obtain the precursor, keep the precursor in an inert gas environment at 400℃ for 6h, and cool to obtain porous flower-like Fe 3 O 4 .
[0025] Carbon-based porous Fe 3 O 4 Preparation: take porous flower-like Fe at a mass ratio of 1:5 3 O 4 、The soluble starch was added to water, stirred rapidly for 30min, and nitrogen was introduced to remove oxygen for 20min, then transferred to the hydrothermal reactor, reacted at 200℃ for 15h, cooled and dried to obtain carbon-based porous Fe 3 O 4 .
[0026] Preparation of magnetic composite powder: Weigh 350g of carbon-based porous Fe 3 O 4 , 330g shell powder, 320g olivine are mixed, water is added to the ball mill and ball milled for 2h to obtain...
Embodiment 2
[0031] Porous Flower Fe 3 O 4 The preparation is the same as in Example 1, carbon-based porous Fe 3 O 4 The preparation is the same as in Example 1.
[0032] Preparation of magnetic composite powder: weigh 450g of carbon-based porous Fe 3 O 4 , 350g of shell powder and 200g of olivine are mixed, and water is added to a ball mill for 1.5h to obtain a magnetic composite powder.
[0033] Preparation of modified filler: weigh 150kg of graphite, 300kg of barite, and 200kg of hematite in a pulverizer to obtain a mixed filler powder, stir and mix the mixed filler powder with 365kg of biogas slurry, and seal and ferment at 35-40℃ After 8 days, the obtained fermented product was centrifuged and sterilized, and 32.5 kg of magnetic composite powder was added and mixed to obtain a modified filler.
[0034] Preparation of anti-segregation agent: Weigh 9.5g of acrylamide or sodium acrylate sulfonate, 25g of TPEG, 0.6g of γ-methacryloxypropyltrimethoxysilane and 25g of deionized water into the reac...
Embodiment 3
[0037] Porous Flower Fe 3 O 4 The preparation is the same as in Example 1, carbon-based porous Fe 3 O 4 The preparation is the same as in Example 1.
[0038] Preparation of magnetic composite powder: weigh 400g of carbon-based porous Fe 3 O 4 , 280g shell powder, 320g olivine are mixed, and water is added to a ball mill for 1.5h to obtain a magnetic composite powder.
[0039] Preparation of modified filler: weigh 150kg of graphite, 350kg of barite, 230kg of hematite, and pulverize in a pulverizer to obtain mixed filler powder. Stir and mix the mixed filler powder with 340kg of biogas slurry, and then seal and ferment at 35-40℃ After 10 days, the obtained fermented product was centrifuged and sterilized, and 36.5 kg of magnetic composite powder was added and mixed to obtain a modified filler.
[0040] Preparation of anti-segregation agent: Weigh 9.5 g of acrylamide or sodium acrylate sulfonate, 20 g of TPEG, 0.8 g of γ-methacryloxypropyl trimethoxysilane and 25 g of deionized water in...
PUM
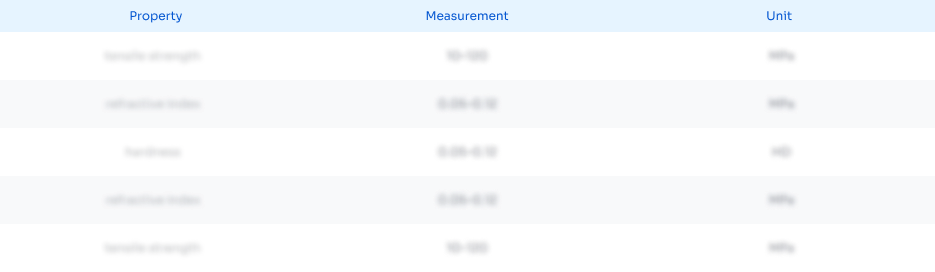
Abstract
Description
Claims
Application Information

- R&D Engineer
- R&D Manager
- IP Professional
- Industry Leading Data Capabilities
- Powerful AI technology
- Patent DNA Extraction
Browse by: Latest US Patents, China's latest patents, Technical Efficacy Thesaurus, Application Domain, Technology Topic, Popular Technical Reports.
© 2024 PatSnap. All rights reserved.Legal|Privacy policy|Modern Slavery Act Transparency Statement|Sitemap|About US| Contact US: help@patsnap.com