High strength lathe tool blade machining technology
A processing technology and high-strength technology, which is applied in the field of high-strength turning tool blade processing technology, can solve the problems of affecting processing quality, poor blade toughness, and easy cracking, and achieve good toughness, long service life, and not easy to break and crack.
- Summary
- Abstract
- Description
- Claims
- Application Information
AI Technical Summary
Problems solved by technology
Method used
Examples
Embodiment 1
[0012] A high-strength turning tool blade processing technology, including the following steps: S1, raw material preparation: select high-speed steel as the raw material of turning tool blade; S2, raw material pretreatment: use the high-speed steel selected in S1 to forge with a forging machine, forging temperature 800°C, cooling naturally after forging to obtain the billet; S3, billet heat treatment: put the billet processed in S2 into a vacuum heating furnace, heat treat the billet, the temperature of the heat treatment is 860°C, the heat treatment The time is 60 minutes, and the billet is naturally cooled after heat treatment; S4, billet cutting: clamp the billet processed in S3 in a high-speed milling machine, debug the milling machine, mill the blade shape, mill the outer contour shape of the blade, and the milling machine speed 22000r / min; S5, blank punching; clamp the blank milled in S4 in the drilling machine, and punch holes; S6, blank blade making: move the blank punc...
Embodiment 2
[0014] A high-strength turning tool blade processing technology, including the following steps: S1, raw material preparation: select high-speed steel as the raw material of turning tool blade; S2, raw material pretreatment: use the high-speed steel selected in S1 to forge with a forging machine, forging temperature 825°C, after forging is naturally cooled to obtain a billet; S3, billet heat treatment: put the billet processed in S2 into a vacuum heating furnace, and heat treat the billet, the temperature of the heat treatment is 900°C, the heat treatment The time is 50 minutes, and the billet is naturally cooled after heat treatment; S4, billet cutting: clamp the billet processed in S3 in a high-speed milling machine, debug the milling machine, mill the blade shape, mill the outer contour shape of the blade, and the milling machine speed 30000r / min; S5, blank punching; clamp the blank milled in S4 in the drilling machine, and punch holes; S6, blank blade making: move the blank ...
Embodiment 3
[0016] A high-strength turning tool blade processing technology, including the following steps: S1, raw material preparation: select high-speed steel as the raw material of turning tool blade; S2, raw material pretreatment: use the high-speed steel selected in S1 to forge with a forging machine, forging temperature 850°C, after forging is naturally cooled to obtain a billet; S3, billet heat treatment: put the billet processed in S2 into a vacuum heating furnace, and heat treat the billet, the temperature of the heat treatment is 950°C, the heat treatment The time is 40 minutes, and the billet is naturally cooled after heat treatment; S4, billet cutting: clamp the billet processed in S3 in a high-speed milling machine, debug the milling machine, perform milling of the blade shape, mill out the shape of the outer contour of the blade, and the rotation speed of the milling machine 40000r / min; S5, blank punching; clamp the blank milled in S4 in the drilling machine, and punch holes...
PUM
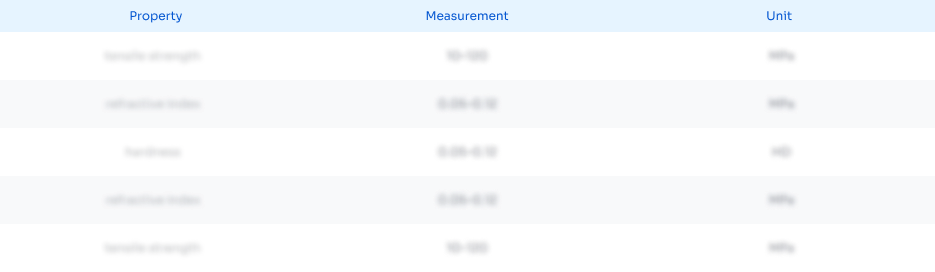
Abstract
Description
Claims
Application Information

- R&D
- Intellectual Property
- Life Sciences
- Materials
- Tech Scout
- Unparalleled Data Quality
- Higher Quality Content
- 60% Fewer Hallucinations
Browse by: Latest US Patents, China's latest patents, Technical Efficacy Thesaurus, Application Domain, Technology Topic, Popular Technical Reports.
© 2025 PatSnap. All rights reserved.Legal|Privacy policy|Modern Slavery Act Transparency Statement|Sitemap|About US| Contact US: help@patsnap.com