A kind of preparation method of diallyl isophthalate
A technology of diallyl isophthalate and dimethyl isophthalate, applied in the field of preparation of diallyl isophthalate, can solve the problem of increasing the process of separating water-carrying agent and the low product yield , long reaction time and other problems, to achieve the effect of saving additive costs, high product yield, and easy recycling
- Summary
- Abstract
- Description
- Claims
- Application Information
AI Technical Summary
Problems solved by technology
Method used
Examples
Embodiment 1
[0019] Add 300 grams of dimethyl isophthalate, 300 grams of propylene alcohol, and 1.5 grams of potassium carbonate powder into the reactor, start stirring, heat up the reaction, control the reaction temperature in the reactor between 90 and 145 ° C, and rectify the column top Temperature is between 60-95°C, heat preservation reaction for 2-4 hours, sampling test, stop heating when the content of dimethyl isophthalate is less than 0.5%, lower the temperature to below 100°C, add 100 grams of water, continue to cool down to 60°C, Add 0.03 g of decolorizing agent, keep stirring for 0.5 hours, add 0.06 g of reducing agent, stir for 0.5 hours, let stand for 30 minutes, separate layers, add 100 g of water for washing, separate layers, heat up and vacuum distill to remove a small amount of water, and obtain the product. The rate is 99.2%.
Embodiment 2
[0020] Example 2: Add 300 grams of dimethyl isophthalate, 450 grams of propylene alcohol, and 4.5 grams of potassium carbonate powder into the reactor, start stirring, heat up the reaction, and control the reaction temperature in the reactor between 90 and 145 ° C. The temperature at the top of the rectification column is between 60 and 95°C, heat preservation reaction for 2-4 hours, take a sample test, stop heating when the content of dimethyl isophthalate is less than 0.5%, lower the temperature to below 100°C, add 150 grams of water, and continue to cool down to 60°C, add 0.015 g of decolorizing agent, keep stirring for 0.5 hours, add 0.003 g of reducing agent, stir for 0.5 hours, let it stand for 30 minutes, separate layers, add 150 g of water to wash, separate layers, heat up and vacuum distill to remove a small amount of water, The product was obtained with a yield of 99.5%.
Embodiment 3
[0021] Example 3: Add 300 grams of dimethyl isophthalate, 360 grams of propylene alcohol, and 3 grams of potassium carbonate powder into the reactor, start stirring, heat up the reaction, and control the reaction temperature in the reactor between 90 and 145 ° C. The temperature at the top of the rectification column is between 60 and 95°C, keep it warm for 2-4 hours, take a sample test, stop heating when the content of dimethyl isophthalate is less than 0.5%, lower the temperature to below 100°C, add 90 grams of water, and continue to cool down to 60°C, add 0.02 g of decolorizing agent, keep stirring for 0.5 hours, add 0.03 g of reducing agent, stir for 0.5 hours, let it stand for 30 minutes, separate layers, add 90 g of water to wash, separate layers, heat up and vacuum distill to remove a small amount of water, The product was obtained with a yield of 99.8%.
PUM
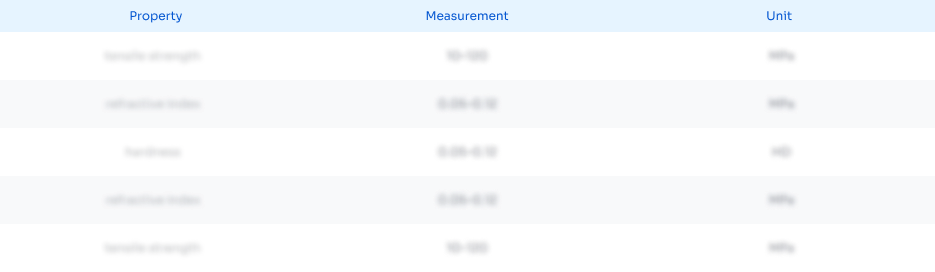
Abstract
Description
Claims
Application Information

- Generate Ideas
- Intellectual Property
- Life Sciences
- Materials
- Tech Scout
- Unparalleled Data Quality
- Higher Quality Content
- 60% Fewer Hallucinations
Browse by: Latest US Patents, China's latest patents, Technical Efficacy Thesaurus, Application Domain, Technology Topic, Popular Technical Reports.
© 2025 PatSnap. All rights reserved.Legal|Privacy policy|Modern Slavery Act Transparency Statement|Sitemap|About US| Contact US: help@patsnap.com