Method for comprehensively recycling valuable components in paigeite
A boronite and component technology, applied in the direction of boron halide compounds, chemical instruments and methods, boron halides, etc., can solve problems such as large pollution, low utilization rate of magnesium, and impact on the environment, so as to promote comprehensive utilization and realize comprehensive utilization. The effect of utilization and low production cost
- Summary
- Abstract
- Description
- Claims
- Application Information
AI Technical Summary
Problems solved by technology
Method used
Examples
Embodiment 1
[0057] Using 1# boronite in a certain place, its chemical composition is TFe:29.23%, Fe 3 o 4 : 26.24%, FeO: 12.87%, B 2 o 3 : 8.03%, MgO: 26.88%, SiO 2 : 12.22%, CaO: 0.35%, other oxides: 13.41%.
[0058] The method for the comprehensive recovery and utilization of valuable components in boron ore comprises the following steps:
[0059] A. Mixing materials: Add mineral powder, low-sulfur coal and calcium oxide into the mixer, the addition of low-sulfur coal is 10% of the total mass of mineral powder, and the addition of calcium oxide is 5% of the total mass of mineral powder. The particle size of mineral powder, low-sulfur coal and calcium oxide is ≤100 mesh, and they are fully mixed.
[0060] B. Reduction of iron oxides: put the mixed powder into a tunnel kiln, heat it to 1200° C. with microwaves, and keep it warm for 0.8 hours to reduce iron oxides to obtain metal sponge iron.
[0061] C. Separation of metal sponge iron: After the reduction, use 1.5T magnetic inductio...
Embodiment 2
[0067] Using 1# boronite in a certain place, its chemical composition is TFe:29.23%, Fe 3 o 4 : 26.24%, FeO: 12.87%, B 2 o 3 : 8.03%, MgO: 26.88%, SiO 2 : 12.22%, CaO: 0.35%, other oxides: 13.41%.
[0068] The method for the comprehensive recovery and utilization of valuable components in boron ore comprises the following steps:
[0069] A. Mixing: Add mineral powder, coke chips, and calcium oxide into the mixer. The amount of coke chips added is 12% of the total mass of mineral powder, and the amount of calcium oxide added is 4% of the total mass of mineral powder. , coke scraps and calcium oxide with a particle size of ≤100 mesh, fully mixed.
[0070] B. Reduction of iron oxides: put the mixed powder into a tunnel kiln, heat it with microwave to 1000°C, and keep it warm for 1 hour to reduce the iron oxides to obtain metal sponge iron.
[0071] C. Separation of metal sponge iron: After the reduction, use 1.2T magnetic induction to separate to obtain metal sponge iron an...
Embodiment 3
[0077] Using 2# boronite in a certain place, its chemical composition is TFe: 26.82%, Fe 3 o 4 : 28.52%, FeO: 6.64%, B 2 o 3 :8.97%, MgO:23.50%, SiO 2 : 18.29%, CaO: 0.72%, other oxides: 13.36%.
[0078] The method for the comprehensive recovery and utilization of valuable components in boron ore comprises the following steps:
[0079] A. Mixing materials: Add mineral powder, low-sulfur coal and calcium oxide into the mixer, the addition of low-sulfur coal is 13% of the total mass of mineral powder, and the addition of calcium oxide is 6% of the total mass of mineral powder. The particle size of mineral powder, low-sulfur coal and calcium oxide is ≤100 mesh, and they are fully mixed.
[0080] B. Reduction of iron oxides: put the mixed powder into a tunnel kiln, heat it with microwave to 1200°C, and keep it warm for 0.5 hours to reduce the iron oxides to obtain metal sponge iron.
[0081] C. Separation of metal sponge iron: After the reduction, use 1.5T magnetic induction...
PUM
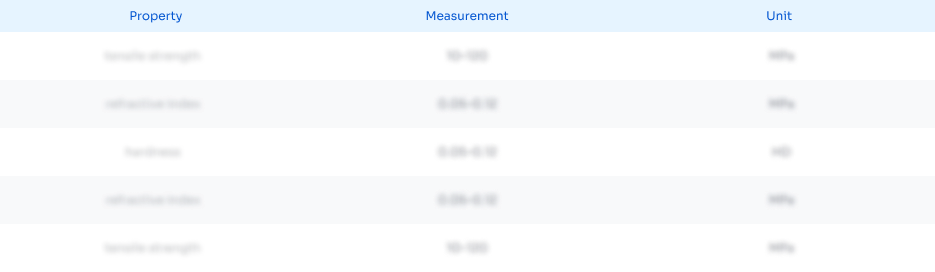
Abstract
Description
Claims
Application Information

- Generate Ideas
- Intellectual Property
- Life Sciences
- Materials
- Tech Scout
- Unparalleled Data Quality
- Higher Quality Content
- 60% Fewer Hallucinations
Browse by: Latest US Patents, China's latest patents, Technical Efficacy Thesaurus, Application Domain, Technology Topic, Popular Technical Reports.
© 2025 PatSnap. All rights reserved.Legal|Privacy policy|Modern Slavery Act Transparency Statement|Sitemap|About US| Contact US: help@patsnap.com