Method of rotary-connection cabin pressure removing of metering feeder and rotary-connection cabin pressure removing dynamic weighing and feeding machine
A feeder and weighing sensor technology, applied in the mechanical field, can solve problems such as spilled materials, waste of manpower and material resources, belt deviation, etc.
- Summary
- Abstract
- Description
- Claims
- Application Information
AI Technical Summary
Problems solved by technology
Method used
Image
Examples
Embodiment 1
[0081] like Figure 1 to Figure 3 As shown, it is the dynamic weighing feeder for rotary-connection and flat-removal of warehouse pressure described in embodiment 1, including rotary connection hanger 5, rotary connection feeder 12, hinge shaft 4, rotary connection weighing feeder 10 , load cell 2, speed sensor 8 and computing unit 1, etc., the rotary hanger 5 and the rotary feeder 12 are separately connected or integrated, when the rotary hanger 5 and the rotary feeder 12 are split When connecting, the lower part of the rotary hanger 5 is provided with the hinged ear 3 of the hanger, the upper part of the rotary feeder 12 is provided with the rotary hinged ear 9 of the hopper, and the bottom of the rotary feeder 12 is provided with a rotary weigher. Conveyor 10, etc., the rotating hanger 5 is hung on the silo mouth 23 or set on the support foundation 14, and the axis of the hanger is screwed and hinged ear hole 11 is set at the middle point of the pressure affected area of ...
Embodiment 2
[0085] like Figure 4 to Figure 8 As shown, it is the dynamic weighing feeder for rotary connection and flat removal of warehouse pressure described in embodiment 2. The rotary connection weighing feeder 10 includes a drum 16, a conveyor belt 15 and a driving device 18, etc., and the speed sensor 8 is arranged on The roller 16 or the speed sensor 8 is set on the conveyor belt 15 or the speed sensor 8 is set on the driving device 18, and the receiving end 17 of the rotary feeder is directly connected with the silo port 23 or the upper part of the rotary feeder 12 is provided with a feeding chute 20. The feeding chute 20 of the rotary feeder 12 is provided with a control gate 19, the feeding chute 20 is connected separately or integrally with the rotary feeder 12, and the weighing sensor 2 is connected with the rotary weighing feeder 10 directly connected or provided with a shock absorber 21, or a shock absorber 21 is provided between the hinged ear 3 and the hinge shaft 4 of th...
Embodiment 3
[0088] like Figure 9 As shown, it is the dynamic weighing feeder described in the embodiment 3, the screw-connected hanger 5 or the screw-connected feeder 12 is provided with a material flow shaper 24 at the butt joint of the screw-connected feeder 12 and the bin mouth 23. , the material flow shaper 24 arranges the shape, flow direction, and flow rate of the material flowing into the rotary weighing conveyor 10, so that the pressure center point of the pressure zone of the material bin 6 is relatively stable, and the support hinge point 7 of the feeder is kept in the bin for a long time. The central point of the bin pressure in the nip area ensures that the bin pressure forces on both sides of the feeder support hinge point 7 are equal in magnitude and balanced with each other during the material flow process.
[0089] All the other are with embodiment 1.
PUM
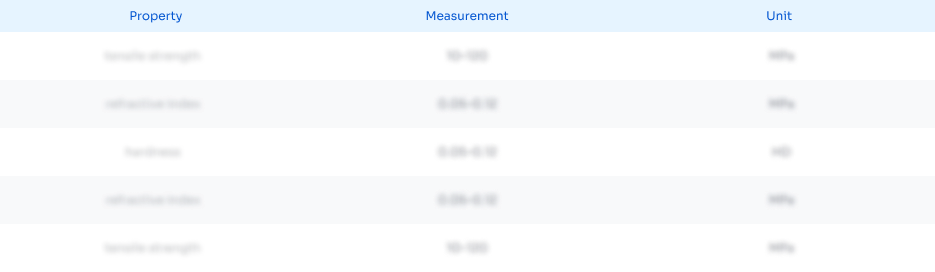
Abstract
Description
Claims
Application Information

- R&D Engineer
- R&D Manager
- IP Professional
- Industry Leading Data Capabilities
- Powerful AI technology
- Patent DNA Extraction
Browse by: Latest US Patents, China's latest patents, Technical Efficacy Thesaurus, Application Domain, Technology Topic, Popular Technical Reports.
© 2024 PatSnap. All rights reserved.Legal|Privacy policy|Modern Slavery Act Transparency Statement|Sitemap|About US| Contact US: help@patsnap.com