Cutter bit for machining ball threads and cutter therefor
A tool head and ball technology, which is applied to tools for lathes, manufacturing tools, metal processing equipment, etc., can solve the problems of high production cost of ball screws, long production cycle of ball screws, and long grinding time. Achieve the effect of saving material cost, reducing turning allowance and reducing contact area
- Summary
- Abstract
- Description
- Claims
- Application Information
AI Technical Summary
Problems solved by technology
Method used
Image
Examples
Embodiment Construction
[0025] The present invention will be further described below in conjunction with the accompanying drawings and specific embodiments.
[0026] like Figure 1-2 As shown, a cutter head for processing ball screw thread includes a body, and the body includes two cutting edges 1, and the cutting edge 1 includes a cutting edge 2 and two side cutting edges 3, and the two side cutting edges 3 are connected to the cutting edge 2 and the body The line connecting the central points is left-right symmetrical. The side edge 3 includes a cutting protrusion 3.1, which is arc-shaped. The line connecting the sharp point of 2 and the central point of the body is the line of symmetry 4, the center of the cutting protrusion 3.1 on the left side of the line of symmetry 4 is on the right side of the line of symmetry 4, and the center of the cutting protrusion 3.1 on the right is on the left of the line of symmetry 4 Side, that is, the cutting protrusion 3.1 on the left side and the line connecting...
PUM
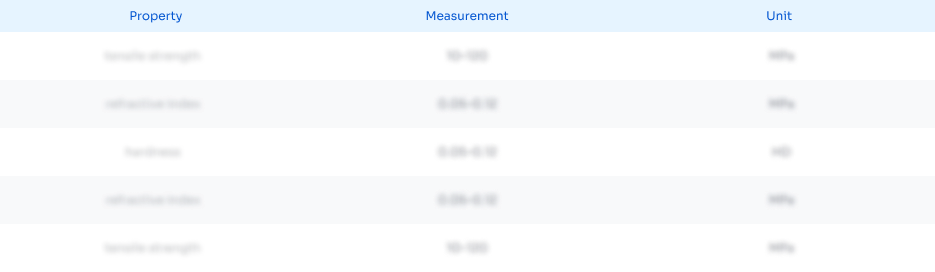
Abstract
Description
Claims
Application Information

- R&D Engineer
- R&D Manager
- IP Professional
- Industry Leading Data Capabilities
- Powerful AI technology
- Patent DNA Extraction
Browse by: Latest US Patents, China's latest patents, Technical Efficacy Thesaurus, Application Domain, Technology Topic, Popular Technical Reports.
© 2024 PatSnap. All rights reserved.Legal|Privacy policy|Modern Slavery Act Transparency Statement|Sitemap|About US| Contact US: help@patsnap.com