Array type ultrasonic dynamic sealing device and method
A sealing device and array technology, which is applied to the sealing of engines, engine components, mechanical equipment, etc., can solve the problems of not very severe sound pressure changes and unsatisfactory sealing effects, and achieve good results, convenient structure and assembly, and reduced The effect of wear and tear
- Summary
- Abstract
- Description
- Claims
- Application Information
AI Technical Summary
Problems solved by technology
Method used
Image
Examples
Embodiment
[0035] An array type ultrasonic dynamic sealing device of the present invention, the backing 6 is formed by hot pressing after fully mixing tungsten powder and epoxy resin, the particle size of the tungsten powder is 5 μm, and the volume fraction is 15%; the outer side of the backing 6 is in contact with the T-shaped groove, Fixed in the sealing sleeve 8 through the T-shaped groove;
[0036] Acoustoelectric chip belt 5 is made up of rectangular PZT piezoelectric ceramic sheet, and the thickness of piezoelectric ceramic sheet is 1 / 2 wavelength when ultrasonic wave propagates in it.
[0037] The matching layer 4 is made of low-viscosity epoxy resin filled with alumina in a single layer, the particle size of alumina powder is 2.5 μm, and the volume fraction is 25%. The filler and the base material are cast into a thin layer by casting. 1 / 4 wavelength when layer 4 propagates; acoustic lens 3 is made of polymethyl methacrylate (PMMA).
[0038] Four radial sealing teeth 10 are even...
PUM
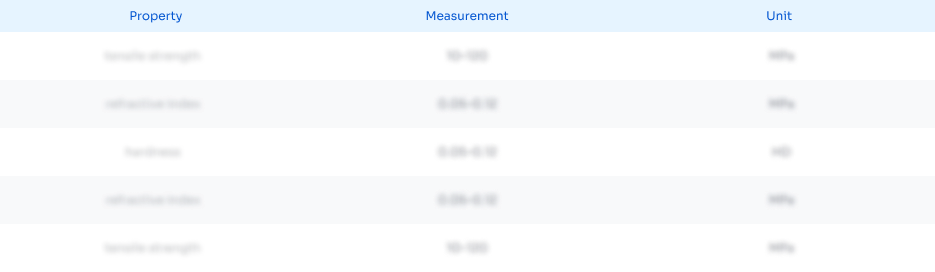
Abstract
Description
Claims
Application Information

- R&D
- Intellectual Property
- Life Sciences
- Materials
- Tech Scout
- Unparalleled Data Quality
- Higher Quality Content
- 60% Fewer Hallucinations
Browse by: Latest US Patents, China's latest patents, Technical Efficacy Thesaurus, Application Domain, Technology Topic, Popular Technical Reports.
© 2025 PatSnap. All rights reserved.Legal|Privacy policy|Modern Slavery Act Transparency Statement|Sitemap|About US| Contact US: help@patsnap.com