Desulphurization method used for pretreatment of molten iron
A technology of molten iron pretreatment and molten iron, applied in the direction of improving process efficiency, etc., can solve the problems of reducing the desulfurization rate of refining furnaces, high slag treatment costs, environmental pollution, etc., to reduce subsequent slag treatment costs, reduce desulfurization costs, and reduce production cost effect
- Summary
- Abstract
- Description
- Claims
- Application Information
AI Technical Summary
Problems solved by technology
Method used
Image
Examples
Embodiment Construction
[0031] In order to make the purpose, technical solution and advantages of the present invention clearer, the technical solution of the present invention will be clearly and completely described below in conjunction with specific embodiments of the present invention and corresponding drawings. Apparently, the described embodiments are only some, not all, embodiments of the present invention. Based on the embodiments of the present invention, all other embodiments obtained by those skilled in the art without making creative efforts fall within the protection scope of the present invention.
[0032] The technical solutions provided by the embodiments of the present invention will be described in detail below in conjunction with the accompanying drawings.
[0033] see figure 1 , the desulfurization method for molten iron pretreatment according to an embodiment of the present invention comprises:
[0034] First, after the continuous casting or die casting, pour the hot slag and c...
PUM
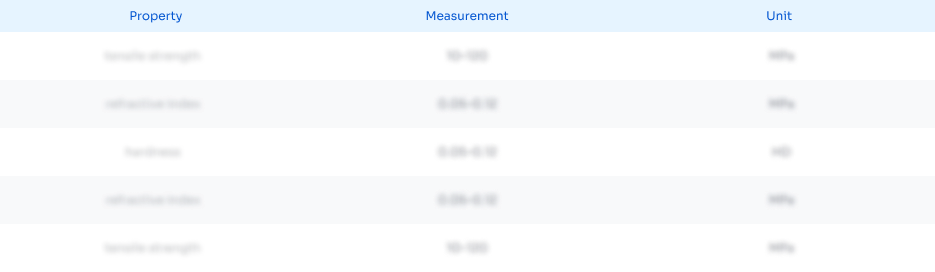
Abstract
Description
Claims
Application Information

- R&D
- Intellectual Property
- Life Sciences
- Materials
- Tech Scout
- Unparalleled Data Quality
- Higher Quality Content
- 60% Fewer Hallucinations
Browse by: Latest US Patents, China's latest patents, Technical Efficacy Thesaurus, Application Domain, Technology Topic, Popular Technical Reports.
© 2025 PatSnap. All rights reserved.Legal|Privacy policy|Modern Slavery Act Transparency Statement|Sitemap|About US| Contact US: help@patsnap.com