Method for gasification dephosphorization and thermal-state cyclic utilization of converter slag
A converter slag and dephosphorization technology, which is applied in the manufacture of converters, etc., can solve the problems of improving dephosphorization effect, increasing carbon emissions, and high cost of solid reductants, and achieves the goal of realizing thermal recycling, reducing carbon emissions, and saving costs Effect
- Summary
- Abstract
- Description
- Claims
- Application Information
AI Technical Summary
Problems solved by technology
Method used
Image
Examples
Embodiment 1
[0040] Using a 210t top-bottom double blowing converter, there are 12 ring-slit ventilation bricks at the bottom, which are evenly arranged in 0.5D concentric circles. After the smelting of the previous furnace, about 15 tons of slag remained, and the phosphorus content in the slag was 0.90%. Add 24 tons of scrap steel, add 186 tons of molten iron, the phosphorus content of molten iron and scrap steel are 0.056% and 0.03% respectively, and the content of silicon in molten iron is 0.5%; start blowing, bottom blow hydrogen, flow rate is 1260Nm 3 / hour, the top blowing oxygen flow is 48000Nm 3 / hour, the gun position is controlled at 1.8-2.2m during the smelting process; after 5 minutes of blowing, the molten steel temperature in the molten pool reaches 1400 °C, the furnace is turned down, and 6 tons of slag is discharged; shake the converter, continue to blow, and blow hydrogen at the bottom. 700Nm 3 / hour, the top blowing oxygen flow is 50000Nm 3 / hour, the gun position is c...
Embodiment 2
[0042] A 210t top-bottom double blowing converter is used, and 16 through-hole ventilation bricks are used at the bottom, which are staggered in the 0.7D and 0.55D concentric circles. After the smelting of the previous furnace, about 16 tons of slag remained, and the phosphorus content in the slag was 0.93%. Add 25 tons of scrap steel, add 185 tons of molten iron, the phosphorus content of molten iron and scrap steel are 0.060% and 0.032% respectively, and the content of silicon in molten iron is 0.55%; start blowing, blow hydrogen at the bottom, and the flow rate is 1890Nm 3 / hour, the top blowing oxygen flow is 46000Nm 3 / hour, the gun position is controlled at 1.9-2.2m during the smelting process; after 5.5 minutes of blowing, the molten steel temperature in the molten pool reaches 1430 ° C, the furnace is turned down, and the slag is 7 tons; shake the converter, continue to blow, and blow hydrogen at the bottom. 1000Nm 3 / hour, the top blowing oxygen flow is 48000Nm 3 / ...
Embodiment 3
[0044] A 210t top-bottom double blowing converter is used, and 20 diffused-type air-permeable bricks are used at the bottom, which are staggered in 0.75D and 0.55D concentric circles. After the smelting of the previous furnace, about 16 tons of slag remained, and the phosphorus content in the slag was 0.88%. . Add 30 tons of scrap steel, add 180 tons of molten iron, the phosphorus content of molten iron and scrap steel are 0.062% and 0.033% respectively, and the silicon content of molten iron is 0.60%; start blowing, blow hydrogen at the bottom, and control the flow rate to 2500Nm 3 / hour, the top blowing oxygen flow is 45000Nm 3 / hour, the gun position is controlled at 1.9-2.3m during the smelting process; after 4.5 minutes of blowing, the molten steel temperature in the molten pool reaches 1390 ° C, the furnace is turned down, and the slag is 8 tons; 1200Nm 3 / hour, the top blowing oxygen flow is 52000Nm 3 / hour, the gun position is controlled to 1.5-2.0m during the smel...
PUM
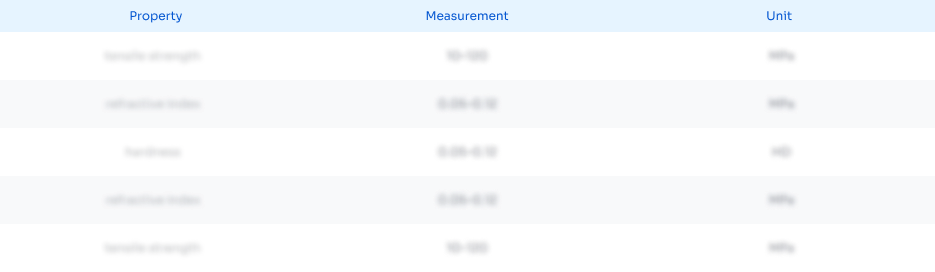
Abstract
Description
Claims
Application Information

- R&D
- Intellectual Property
- Life Sciences
- Materials
- Tech Scout
- Unparalleled Data Quality
- Higher Quality Content
- 60% Fewer Hallucinations
Browse by: Latest US Patents, China's latest patents, Technical Efficacy Thesaurus, Application Domain, Technology Topic, Popular Technical Reports.
© 2025 PatSnap. All rights reserved.Legal|Privacy policy|Modern Slavery Act Transparency Statement|Sitemap|About US| Contact US: help@patsnap.com