Radiant pipe combustion performance thermal simulation test furnace and method
A combustion performance and radiant tube technology, applied in the direction of combustion method, burner, combustion type, etc., can solve the problem of difficult detection of radiant tube flame combustion state, achieve the effects of reducing emissions, reducing fuel consumption, and improving combustion efficiency
- Summary
- Abstract
- Description
- Claims
- Application Information
AI Technical Summary
Problems solved by technology
Method used
Image
Examples
Embodiment 1
[0049] The cold-rolled continuous annealing furnace with an annual output of 500,000 tons uses mixed gas fuel. The W-type radiant tube is installed in a thermal simulation experimental furnace, and the same mixed gas is used as fuel to test the thermal performance of the radiant tube combustion. 40 thermocouples are used to detect the uniformity of the wall temperature of the radiant tube, and to detect the thermal efficiency of the radiant tube, the thermal efficiency of the heat exchanger, and the amount of backflow flue gas. Through thermal performance testing, its air-fuel ratio and suction parameters are optimized. The optimized parameters are applied in actual production, reducing the unit consumption of the continuous annealing furnace from 0.927GJ / t to 0.895GJ / t, which is a reduction of 3.45%, and the NOx emission is reduced from the original 105ppm to 79ppm.
Embodiment 2
[0051] A silicon steel factory uses coke oven gas as the fuel drying furnace, and the U-shaped radiant tube it uses is installed in the thermal simulation experimental furnace. The same coke oven gas is used as the fuel to test the thermal performance of the radiant tube combustion. 30 thermocouples are used to detect the uniformity of the wall temperature of the radiant tube, and the thermal efficiency of the radiant tube and the heat exchanger are also tested. Through the thermal performance test, the thermal parameters are obtained, which are used in the development and manufacture of a new type of radiant tube complete set of high-efficiency and low-nitrogen large reflux flue gas circulation. After the new product is actually applied, the combustion efficiency of the radiant tube is 99.9%, the thermal efficiency of the radiant tube is greater than 70%, and the maximum temperature difference of the radiant tube wall is less than 100°C.
Embodiment 3
[0053] The hot-dip galvanizing continuous annealing furnace with an annual output of 620,000 tons uses mixed gas as fuel. The W-type radiant tube used in it was installed on the thermal simulation experimental furnace, and the same mixed gas was used as fuel to test the combustion performance of the radiant tube heating. 40 thermocouples are used to detect the uniformity of the wall temperature of the radiant tube, and the thermal efficiency of the radiant tube and the heat exchanger are also tested. Through thermal performance testing, the air-fuel ratio combustion parameters are optimized, the heating capacity of the radiant tube in the F2 section is improved, and the production energy efficiency of the hot-dip galvanizing continuous annealing furnace is increased by 1.1%.
PUM
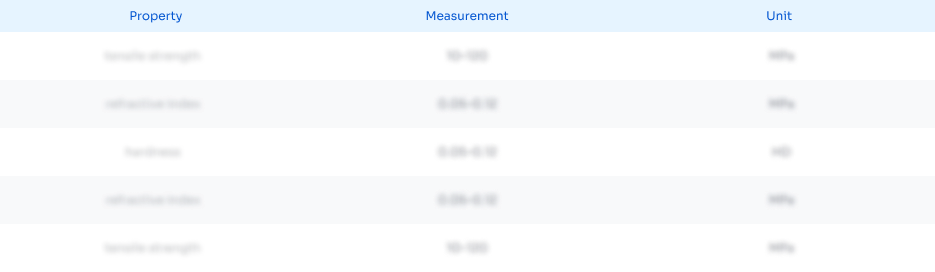
Abstract
Description
Claims
Application Information

- Generate Ideas
- Intellectual Property
- Life Sciences
- Materials
- Tech Scout
- Unparalleled Data Quality
- Higher Quality Content
- 60% Fewer Hallucinations
Browse by: Latest US Patents, China's latest patents, Technical Efficacy Thesaurus, Application Domain, Technology Topic, Popular Technical Reports.
© 2025 PatSnap. All rights reserved.Legal|Privacy policy|Modern Slavery Act Transparency Statement|Sitemap|About US| Contact US: help@patsnap.com