Application of graphite in preparation of chip cooling heat sink material
A chip heat dissipation and graphite technology, applied in electrical components, electrical solid devices, circuits, etc., can solve the problem of heat accumulation and other problems, and achieve the effect of low cost and simple preparation process
- Summary
- Abstract
- Description
- Claims
- Application Information
AI Technical Summary
Problems solved by technology
Method used
Image
Examples
Embodiment Construction
[0018] In order to fully understand the technical content of the present invention, the technical solutions of the present invention will be further introduced and illustrated below in conjunction with specific examples, but not limited thereto.
[0019] The invention provides an application of graphite in the preparation of heat sink materials for chips. Graphite is used as the heat sink substrate material for chips. The crystal lamellar structure of graphite determines that its thermal conductivity in a specific direction is very high, and its heat capacity The value is very low, there is no heat accumulation phenomenon, and heat can be quickly transferred to surrounding substances, including air. Specifically, the performance list of the graphite compared with the main heat sink substrate materials at this stage is as follows:
[0020]
[0021] Specifically, the graphite of the present invention is mainly used as a heat sink substrate material for chips with high injectio...
PUM
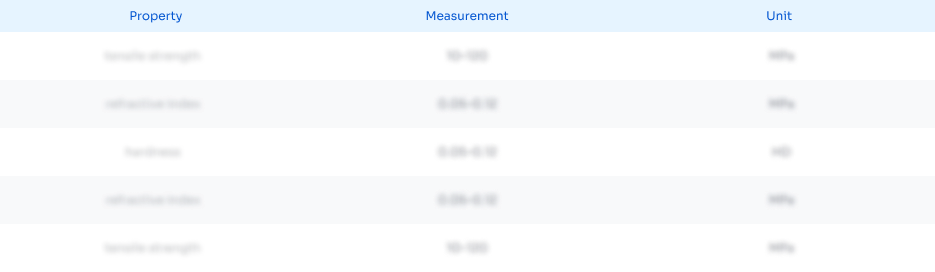
Abstract
Description
Claims
Application Information

- Generate Ideas
- Intellectual Property
- Life Sciences
- Materials
- Tech Scout
- Unparalleled Data Quality
- Higher Quality Content
- 60% Fewer Hallucinations
Browse by: Latest US Patents, China's latest patents, Technical Efficacy Thesaurus, Application Domain, Technology Topic, Popular Technical Reports.
© 2025 PatSnap. All rights reserved.Legal|Privacy policy|Modern Slavery Act Transparency Statement|Sitemap|About US| Contact US: help@patsnap.com