Ultrathick normalizing high-intensity pressure container steel plate and production method thereof
A steel plate production method and pressure vessel technology, which are applied in the field of steel products, can solve the problems of not being able to improve the rolled strength and thermal strength of steel plates, and cannot guarantee mechanical properties, so as to achieve good internal quality, good lamellar tear resistance, The effect of high production costs
- Summary
- Abstract
- Description
- Claims
- Application Information
AI Technical Summary
Problems solved by technology
Method used
Image
Examples
Embodiment 1
[0021] The P355GH extra-thick normalizing high-strength container steel of this embodiment is prepared from the following components by mass percentage:
[0022] C
Si
mn
P
S
Nb
0.19%
0.30%
1.49%
0.008%
0.001%
0.032%
Ni
Ti
V
Cr
Cu
Alt
0.22%
0.021%
0.013%
0.22%
0.019%
0.042%
[0023] Others are Fe and unavoidable impurities.
[0024] The production preparation method of the P355GH extra thick pressure vessel steel of the present embodiment is as follows:
[0025] 1) Smelting process: After the raw material molten iron is pretreated, it is smelted in a 120t top-bottom combined blowing converter. After the converter is tapped, the ladle is blown with argon for 15 minutes and fed with aluminum wire for deoxidation treatment. The molten steel is sent to the LF refining furnace for refining, and then vacuumed in the VD furnace. For treatment, keep the vacuum for 15 minutes, feed calcium...
Embodiment 2
[0036] The P355GH extra-thick normalizing high-strength container steel of this embodiment is prepared from the following components in mass percentage
[0037] C
Si
mn
P
S
Nb
0.20%
0.30%
1.60%
0.008%
0.001%
0.036%
Ni
Ti
V
Cr
Cu
Alt
0.24%
0.025%
0.016%
0.24%
0.019%
0.042%
[0038] Others are Fe and unavoidable impurities.
[0039] The production and preparation method of the P355GH extra-thick normalizing high-strength container steel in this embodiment is the same as in Example 1, the difference is that the thickness of the raw material billet after vacuum electron beam welding of the three-layer continuous casting billet is 830mm, and the heating time of the composite billet in the heating furnace is 23 Hour.
[0040]
[0041] The normalizing temperature is 912°C, and the time in the furnace is 230 minutes.
[0042] Such as figure 2 Shown: the metallographic structure at ...
Embodiment 3
[0044] The P355GH extra-thick normalizing high-strength container steel of this embodiment is prepared from the following components by mass percentage:
[0045] C
Si
mn
P
S
Nb
0.21%
0.30%
1.65%
0.008%
0.001%
0.038%
Ni
Ti
V
Cr
Cu
Alt
0.28%
0.029%
0.019%
0.28%
0.019%
0.042%
[0046] Others are Fe and unavoidable impurities.
[0047] The production and preparation method of the P355GH extra-thick normalizing high-strength container steel in this embodiment is the same as in Example 1, the difference is that the thickness of the raw material billet after vacuum electron beam welding of the 3-layer continuous casting billet is 840mm, and the heating time of the composite billet in the heating furnace is 24 Hour.
[0048]
[0049] The normalizing temperature is 909°C, and the furnace time is 260 minutes.
PUM
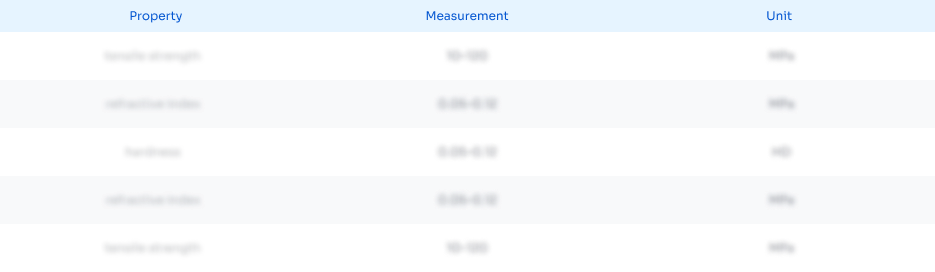
Abstract
Description
Claims
Application Information

- Generate Ideas
- Intellectual Property
- Life Sciences
- Materials
- Tech Scout
- Unparalleled Data Quality
- Higher Quality Content
- 60% Fewer Hallucinations
Browse by: Latest US Patents, China's latest patents, Technical Efficacy Thesaurus, Application Domain, Technology Topic, Popular Technical Reports.
© 2025 PatSnap. All rights reserved.Legal|Privacy policy|Modern Slavery Act Transparency Statement|Sitemap|About US| Contact US: help@patsnap.com