Method for recycling zinc from zinc ferrite resources utilizing ore phase reconstruction method
A zinc ferrite and resource technology, applied in the field of zinc recovery, can solve the problems of not developing a clean and efficient utilization method for zinc recovery, inability to effectively recover and reuse resources, waste of resources and the like, and achieve easy subsequent separation of zinc and iron and good conversion effect. , The effect of low process energy consumption
- Summary
- Abstract
- Description
- Claims
- Application Information
AI Technical Summary
Problems solved by technology
Method used
Image
Examples
Embodiment 1
[0030] Zinc-containing dust (TZn 5.67%, ZnFe 2 o 4 55.72%), crush the raw ore to -1mm, add calcium carbonate, control the molar ratio of effective CaO content in calcium carbonate to zinc ferrite to 2.4:1, mix well and granulate into small balls of 3-20mm, mix The material is placed in a rotary kiln for calcification roasting, the roasting temperature is 1230°C, the roasting time is 15min, and the calcified roasted product is placed in the P(CO) / P(CO+N 2 ) = 40% reduction atmosphere for reduction roasting, the roasting temperature is 800 ° C, the roasting time is 90min, the reduction roasted product is cooled, crushed to -1mm, zinc and iron are separated by magnetic separation, the magnetic field strength is 0.2T, and the magnetic field is 0.2T. The recovery rate of zinc in the tailings is 95.31%.
Embodiment 2
[0032] Zinc-containing dust (TZn 5.67%, ZnFe 2 o 4 55.72%), crush the raw ore to -1mm, add calcium oxide, control the molar ratio of effective CaO content to zinc ferrite to 2.2:1, mix well and granulate into small balls of 3-20mm, place the mixture in Carry out calcification roasting in a rotary kiln, the roasting temperature is 1250°C, the roasting time is 10min, and the calcification roasting product is placed in P(CO) / P(CO+N 2 ) = 40% reduction atmosphere for reduction roasting, the roasting temperature is 850 ° C, the roasting time is 90min, the reduction roasted product is cooled, crushed to -1mm, zinc and iron are separated by magnetic separation, the magnetic field strength is 0.2T, and the magnetic field is 0.2T. The recovery rate of zinc in the tailings is 96.87%.
Embodiment 3
[0034] Zinc-containing dust (TZn 5.67%, ZnFe 2 o 4 55.72%), crush the raw ore to -1mm, add calcium hydroxide, control the molar ratio of effective CaO content in calcium hydroxide to zinc ferrite to 2.0:1, mix well and granulate into small balls of 3-20mm, Put the mixture in a rotary kiln for calcification roasting, the roasting temperature is 1280°C, the roasting time is 5min, and the calcified roasted product is placed in P(CO) / P(CO+N 2 ) = 45% reduction atmosphere for reduction roasting, the roasting temperature is 850 ° C, the roasting time is 90min, the reduction roasted product is cooled, crushed to -1mm, zinc and iron are separated by magnetic separation, the magnetic field strength is 0.2T, and the magnetic field is 0.2T. The recovery rate of zinc in the tailings is 96.06%.
PUM
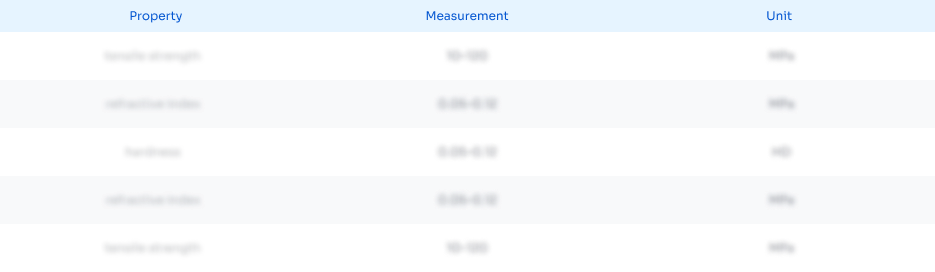
Abstract
Description
Claims
Application Information

- R&D
- Intellectual Property
- Life Sciences
- Materials
- Tech Scout
- Unparalleled Data Quality
- Higher Quality Content
- 60% Fewer Hallucinations
Browse by: Latest US Patents, China's latest patents, Technical Efficacy Thesaurus, Application Domain, Technology Topic, Popular Technical Reports.
© 2025 PatSnap. All rights reserved.Legal|Privacy policy|Modern Slavery Act Transparency Statement|Sitemap|About US| Contact US: help@patsnap.com