Production technology of rock wool
A production process, rock wool technology, applied in the direction of glass production, manufacturing tools, furnace types, etc., can solve the problems of cumbersome process, compressed cupola production of rock wool living space, complexity, etc., to achieve easy-to-obtain components and save waste gas treatment cost, ease of handling
- Summary
- Abstract
- Description
- Claims
- Application Information
AI Technical Summary
Problems solved by technology
Method used
Examples
Embodiment 1
[0026] A production process of rock wool, the steps of which include:
[0027] (1) Prepare raw materials: take each component by mass percentage;
[0028] (2) Raw material melting: Put the raw material into the electric furnace and melt it into magma;
[0029] (3) Centrifuge into fibers: throw the magma into fibers through a centrifuge, and collect the fibers;
[0030] (4) Cotton felt forming: the collected fibers are spread on the pendulum paver, and formed into cotton felt by the forming conveyor;
[0031] (5) Cotton board forming: the cotton felt is pleated, pressurized, dried and solidified to obtain a cotton board;
[0032] (6) Cutting: Cut the cotton board into specified size.
[0033] In step (1), the mass percent of each component contained in the raw material is as follows:
[0034] Dolomite: 10%;
[0035] Basalt: 40%;
[0036] Blast furnace slag: 40%;
[0037] Waste residue: 10%.
[0038] In step (2), the power supply voltage of the electric furnace is 100V. ...
Embodiment 2
[0046] A production process of rock wool, the steps of which include:
[0047] (1) Prepare raw materials: take each component by mass percentage;
[0048] (2) Raw material melting: Put the raw material into the electric furnace and melt it into magma;
[0049] (3) Centrifuge into fibers: throw the magma into fibers through a centrifuge, and collect the fibers;
[0050] (4) Cotton felt forming: the collected fibers are spread on the pendulum paver, and formed into cotton felt by the forming conveyor;
[0051] (5) Cotton board forming: the cotton felt is pleated, pressurized, dried and solidified to obtain a cotton board;
[0052] (6) Cutting: Cut the cotton board into specified size.
[0053] In step (1), the mass percent of each component contained in the raw material is as follows:
[0054] Dolomite: 20%;
[0055] Basalt: 50%;
[0056] Blast furnace slag: 25%;
[0057] Waste residue: 5%.
[0058] In step (2), the power supply voltage of the electric furnace is 100V. ...
Embodiment 3
[0066] A production process of rock wool, the steps of which include:
[0067] (1) Prepare raw materials: take each component by mass percentage;
[0068] (2) Raw material melting: Put the raw material into the electric furnace and melt it into magma;
[0069] (3) Centrifuge into fibers: throw the magma into fibers through a centrifuge, and collect the fibers;
[0070] (4) Cotton felt forming: the collected fibers are spread on the pendulum paver, and formed into cotton felt by the forming conveyor;
[0071] (5) Cotton board forming: the cotton felt is pleated, pressurized, dried and solidified to obtain a cotton board;
[0072] (6) Cutting: Cut the cotton board into specified size.
[0073] In step (1), the mass percent of each component contained in the raw material is as follows:
[0074] Basalt: 90%;
[0075] Blast furnace slag: 10%;
[0076] In step (2), the power supply voltage of the electric furnace is 100V.
[0077] The centrifuge in step (3) is a four-roller c...
PUM
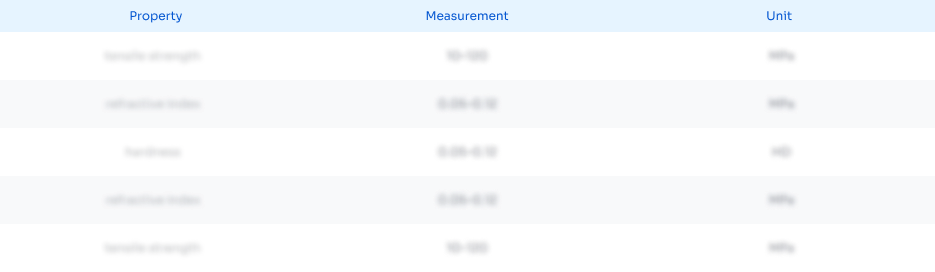
Abstract
Description
Claims
Application Information

- R&D
- Intellectual Property
- Life Sciences
- Materials
- Tech Scout
- Unparalleled Data Quality
- Higher Quality Content
- 60% Fewer Hallucinations
Browse by: Latest US Patents, China's latest patents, Technical Efficacy Thesaurus, Application Domain, Technology Topic, Popular Technical Reports.
© 2025 PatSnap. All rights reserved.Legal|Privacy policy|Modern Slavery Act Transparency Statement|Sitemap|About US| Contact US: help@patsnap.com