Methanol steam reforming hydrogen production copper-based catalyst activation method
A technology for copper-based catalysts and steam reforming, applied in catalyst regeneration/reactivation, chemical instruments and methods, metal/metal oxide/metal hydroxide catalysts, etc. Problems such as process control and cumbersome operation process, to achieve the effect of simple and fast operation of the activation process, low requirements for heating and control equipment, and simple heating procedure
- Summary
- Abstract
- Description
- Claims
- Application Information
AI Technical Summary
Problems solved by technology
Method used
Image
Examples
Embodiment 1
[0022] The activation and reaction pressure of this embodiment is normal pressure.
[0023] Add 50g of reforming catalyst in the fixed bed reactor, the weight percentage of copper oxide in the catalyst is 55%, then the feed preheater and the reactor are heated up, wherein the reactor bed is heated from normal temperature to 230°C for 60min, and the temperature is kept constant. The feed preheater is heated up to 170°C synchronously, and then the catalyst is activated by feeding methanol aqueous solution. The molar ratio of methanol to water is 1, and the hourly space velocity of the methanol aqueous solution is 0.02h. -1 At the same time, the gas composition at the outlet of the gas-liquid separator is analyzed, and the analysis and sampling are performed once every 1 hour. After the hydrogen content in the gas remains stable, the methanol solution feed is turned off. The entire activation process takes 14 hours. Adjust the temperature of the reactor to 280°C and the temperatu...
Embodiment 2
[0025] The activation and reaction pressure of this embodiment is 0.1 MPa (gauge pressure).
[0026] Add 100g of reforming catalyst into the fixed bed reactor, the weight percentage of copper oxide in the catalyst is 60%, then the feed preheater and the reactor are heated up, wherein the reactor bed is heated from normal temperature to 240°C for 90 minutes, and the temperature is kept constant. Raise the temperature of the feed preheater to 150°C synchronously, and then feed the methanol aqueous solution to activate the catalyst. The molar ratio of methanol to water is 0.5, and the hourly space velocity of the methanol aqueous solution is 0.03h -1 At the same time, analyze the gas composition at the outlet of the gas-liquid separator, and analyze and sample once every 1 hour. After the hydrogen content in the gas remains stable, turn off the feeding of the methanol solution, and the entire activation takes 16 hours. Adjust the temperature of the reactor to 280°C and the temper...
Embodiment 3
[0028] Add 50g of reforming catalyst in the fixed bed reactor, the weight percentage of copper oxide in the catalyst is 55%, then the feed preheater and the reactor are heated up, wherein the reactor bed is heated from normal temperature to 230°C for 60min, and the temperature is kept constant. Raise the temperature of the feed preheater to 150°C synchronously, and then feed the methanol aqueous solution to activate the catalyst. The molar ratio of methanol to water is 0.1, and the hourly space velocity of the methanol aqueous solution is 0.10h -1 At the same time, analyze the gas composition at the outlet of the gas-liquid separator, and analyze and sample once every 1 hour. After the hydrogen content in the gas remains stable, turn off the feeding of the methanol solution, and the entire activation takes 16 hours. Adjust the temperature of the reactor to 280°C and the temperature of the preheater to 240°C, then feed 54% (weight) methanol solution, and the hourly space velocit...
PUM
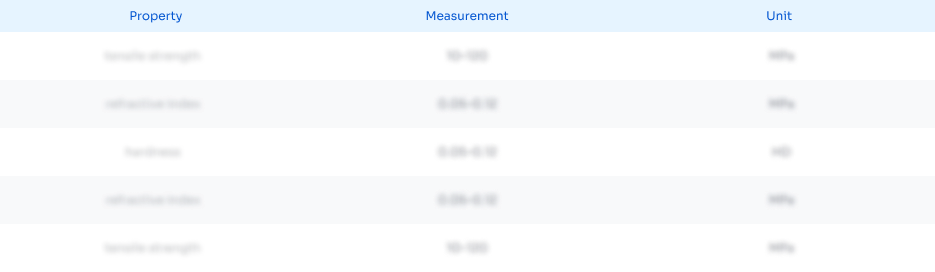
Abstract
Description
Claims
Application Information

- R&D
- Intellectual Property
- Life Sciences
- Materials
- Tech Scout
- Unparalleled Data Quality
- Higher Quality Content
- 60% Fewer Hallucinations
Browse by: Latest US Patents, China's latest patents, Technical Efficacy Thesaurus, Application Domain, Technology Topic, Popular Technical Reports.
© 2025 PatSnap. All rights reserved.Legal|Privacy policy|Modern Slavery Act Transparency Statement|Sitemap|About US| Contact US: help@patsnap.com