Lithium ion battery, negative electrode, negative electrode conductive paste and preparation method of negative electrode conductive paste
A lithium-ion battery and conductive paste technology, applied in electrode manufacturing, battery electrodes, secondary batteries, etc., can solve the problems of electrode sheet quality degradation, difficult to remove air bubbles, etc., and fully guarantee the quality of electrode sheets and load uniformity , improve energy density, good effect of component dispersion
- Summary
- Abstract
- Description
- Claims
- Application Information
AI Technical Summary
Problems solved by technology
Method used
Image
Examples
Embodiment 1
[0059] At room temperature, mix thickener CMC powder and ultrapure deionized water at a ratio of 2:98, and stir in a planetary mixer at 500r / min rotation and 50r / min revolution for 6 hours at room temperature to obtain a transparent viscous colloidal solution. Add the remaining components sequentially in the following proportions, mass ratio thickener CMC: active material micron silicon / silicon nitride / graphite (Si:Si 3 N 4 : C=76.8%: 10.4%: 12.8%): Micron-sized silicon / silicon carbide / graphite (Si:SiC:C=70%: 21%: 9%): Conductive agent KS-15: Binder SBR: Disinfectant Foaming agent EC=1%: 45%: 40%: 3%: 10%: 1%, after adding the active material micron silicon / silicon nitride / graphite and micron silicon / silicon carbide / graphite mixture, the rotation speed is 500r / min , revolution 50r / min and stir at room temperature for 1h, add conductive agent KS-15, rotate at 500r / min, revolution at 50r / min, stir at room temperature for 1h, add binder SBR, rotate at 200r / min, revolution at 20r...
Embodiment 2
[0061]At room temperature, mix the thickener CMC powder and ultrapure deionized water at a ratio of 2:98, and stir in a planetary mixer at 500r / min and 50r / min for 2h at 50°C to obtain a transparent viscous colloidal solution. The remaining components are added in sequence in the following proportions, mass ratio thickener CMC: active material micron-sized silicon / silicon carbide / graphite (Si:SiC:C=70%:21%:9%): conductive agent SPG-6: sticky Binder LA132: defoamer PC=0.5%: 52%: 40%: 3.5%: 3.5%: 0.5%, after adding active material micron-sized silicon / silicon carbide / graphite, the rotation is 400r / min, and the revolution is 40r / min at room temperature Stir for 3 hours, add conductive agent SPG-6, stir at 400r / min and 40r / min at room temperature for 0.5h, add binder LA132, stir at low speed at 150r / min and 15r / min for 0.5h, add defoamer After PC, rotate at 150r / min, rotate at 15r / min and stir at low speed for 0.2h, make up the required amount of solvent ultra-pure deionized water...
Embodiment 3
[0063] At room temperature, mix the thickener CMC powder and ultrapure deionized water at a ratio of 2:98, and stir in a planetary mixer at 300r / min and 30r / min at 60°C for 3h to obtain a transparent viscous colloidal solution. Add the remaining components sequentially in the following proportions, mass ratio thickener CMC: active material micron-sized silicon / silicon oxide / graphite (Si:SiO:C=75%:16%:9%):micron-sized silicon / silicon carbide / Graphite (Si:SiC:C=70%: 21%: 9%): conductive agent VGCF: SPG-15: binder LA133N: defoamer EC=0.5%: 47%: 47%: 0.5%: 1 %: 3%: 1%, add the active material micron-sized silicon / silicon oxide / graphite and micron-sized silicon / silicon carbide / graphite mixture, then rotate at 350r / min, revolution at 35r / min and stir at room temperature for 2.5h, then add conductive agent VGCF After adding the SPG-15 mixture, stir at 500r / min and 50r / min at room temperature for 1h, add binder LA133N, stir at 200r / min and 20r / min at low speed for 0.2h, add defoamer ...
PUM
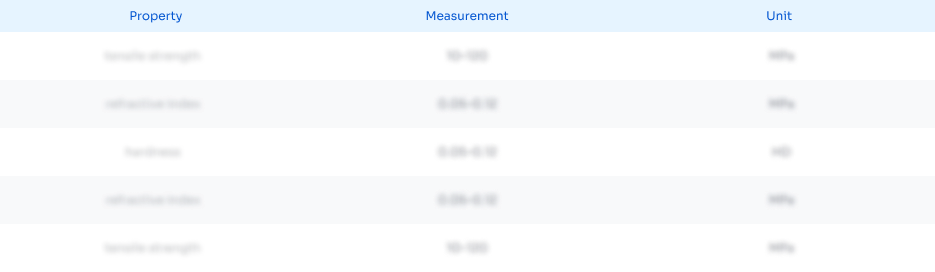
Abstract
Description
Claims
Application Information

- Generate Ideas
- Intellectual Property
- Life Sciences
- Materials
- Tech Scout
- Unparalleled Data Quality
- Higher Quality Content
- 60% Fewer Hallucinations
Browse by: Latest US Patents, China's latest patents, Technical Efficacy Thesaurus, Application Domain, Technology Topic, Popular Technical Reports.
© 2025 PatSnap. All rights reserved.Legal|Privacy policy|Modern Slavery Act Transparency Statement|Sitemap|About US| Contact US: help@patsnap.com