Method and system for predicting residual stress of aluminum alloy large component
A technology of aluminum alloy components and residual stress, which is applied in special data processing applications, instruments, electrical digital data processing, etc., can solve the problem of inability to accurately predict residual stress, etc. Effect
- Summary
- Abstract
- Description
- Claims
- Application Information
AI Technical Summary
Problems solved by technology
Method used
Image
Examples
specific Embodiment approach 1
[0026] Specific Embodiment 1: The method for predicting the residual stress of aluminum alloy large-scale components according to this embodiment, such as figure 1 shown, including:
[0027] Step 1. Install a thermocouple in the aluminum alloy component, heat the aluminum alloy component to the solid solution temperature and keep it uniform, then quench it, and record the temperature change of the thermocouple; generate the temperature field of the aluminum alloy component according to the temperature change of the thermocouple change results.
[0028] The schematic diagram of setting thermocouples in aluminum alloy components is as follows figure 2 as shown, figure 2 The middle cube represents the aluminum alloy component sample. Thermocouples are inserted in different positions of the temperature measuring device, and the cooling curve during the quenching process can be drawn through the temperature measurement results of the thermocouples.
[0029] Step 2: applying th...
specific Embodiment approach 2
[0032] Specific implementation mode two: the difference between this implementation mode and specific implementation mode one is:
[0033] The stress evolution during quenching usually results from the uneven distribution of thermal strain caused by the uneven distribution of the transient temperature field in the aluminum alloy component during quenching. Prediction of quenching stress requires accurate calculation of temperature field. The accurate calculation of the component temperature field depends on the calculation of the heat transfer coefficient of the quenched surface. The calculation of the temperature field in the quenching process (step 1) is specifically:
[0034] Step one, such as figure 2 As shown, thermocouples are installed at multiple preset positions in the aluminum alloy components, and the thermocouples are connected to the data acquisition system. The aluminum alloy components are placed in the heating device and heated to the solid solution temperat...
specific Embodiment approach 3
[0047] Specific implementation mode three: the difference between this implementation mode and specific implementation mode one or two is: in step one and three, the convergence criterion is:
[0048]
[0049] In the formula, N is the number of test points; T i is the measured value of step i; T i ' is the calculated value of step i.
[0050] During the calculation, when f(x) is less than a preset value, it is considered to be convergent. For example, when f(x) is less than a minimum value (1×10 -6 ), the solution process is considered to be convergent, and the calculation ends.
[0051] Other steps and parameters are the same as those in Embodiment 1 or Embodiment 2.
PUM
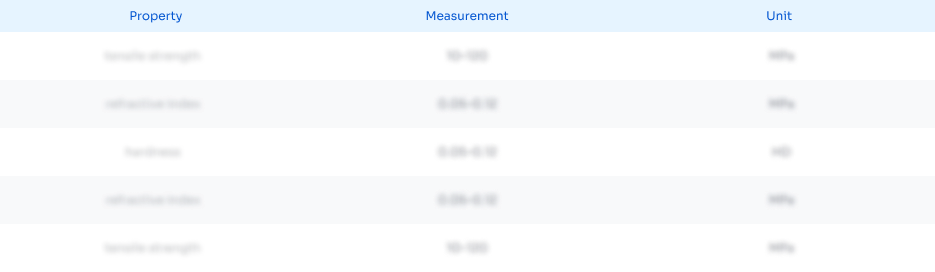
Abstract
Description
Claims
Application Information

- Generate Ideas
- Intellectual Property
- Life Sciences
- Materials
- Tech Scout
- Unparalleled Data Quality
- Higher Quality Content
- 60% Fewer Hallucinations
Browse by: Latest US Patents, China's latest patents, Technical Efficacy Thesaurus, Application Domain, Technology Topic, Popular Technical Reports.
© 2025 PatSnap. All rights reserved.Legal|Privacy policy|Modern Slavery Act Transparency Statement|Sitemap|About US| Contact US: help@patsnap.com