Sc and Hf-contained iron alloy for hot-dip galvanizing anti-vibration iron crucible
A hot-dip galvanized and anti-vibration technology, applied in the field of alloys, can solve the problem of only 2.5 months of service life, and achieve the effects of excellent welding performance, shortening service life, and improving corrosion resistance and wear resistance.
- Summary
- Abstract
- Description
- Claims
- Application Information
AI Technical Summary
Problems solved by technology
Method used
Examples
Embodiment 1
[0017] An iron alloy containing Sc and Hf for hot-dip galvanized anti-vibration iron pan at 360-450 degrees. In terms of weight percentage, the chemical composition of the alloy is: Ca: 0.3wt.%, Bi: 0.6wt.%, Ge: 0.2wt.%, Sc: 0.2wt.%, Hf: 0.2wt.%, W: 0.3wt .%, the balance is iron. Alloy preparation method: Add the above-mentioned raw materials into an argon-protected induction furnace, and use a silicon carbide crucible; induction heating to 1500-1600 degrees to form an alloy solution, and use the electromagnetic stirring effect to fully stir for about 10 minutes; The alloy liquid is kept at 1500-1600 degrees for 10 minutes and then cast into the required round ingot. The obtained ingot is hot-rolled at 800 degrees, and the rolling reduction in each pass is 10-15%. After every two hot rollings, the intermediate annealing temperature is 900 degrees, and the temperature is kept for 1 hour. Finally, the material is rolled into a steel plate with a thickness of 40-60mm, and the ...
Embodiment 2
[0020] An iron alloy containing Sc and Hf for hot-dip galvanized anti-vibration iron pan at 360-450 degrees. In terms of weight percentage, the chemical composition of the alloy is: Ca: 0.5wt.%, Bi: 0.8wt.%, Ge: 0.5wt.%, Sc: 0.3wt.%, Hf: 0.5wt.%, W: 0.5wt .%, the balance is iron. Alloy preparation method: Add the above-mentioned raw materials into an argon-protected induction furnace, and use a silicon carbide crucible; induction heating to 1500-1600 degrees to form an alloy solution, and use the electromagnetic stirring effect to fully stir for about 10 minutes; The alloy liquid is kept at 1500-1600 degrees for 10 minutes and then cast into the required round ingot. The obtained ingot is hot-rolled at 800 degrees, and the rolling reduction in each pass is 10-15%. After every two hot rollings, the intermediate annealing temperature is 900 degrees, and the temperature is kept for 1 hour. Finally, the material is rolled into a steel plate with a thickness of 40-60mm, and the ...
Embodiment 3
[0023] An iron alloy containing Sc and Hf for hot-dip galvanized anti-vibration iron pan at 360-450 degrees. In terms of weight percentage, the chemical composition of the alloy is: Ca: 0.4wt.%, Bi: 0.7wt.%, Ge: 0.3wt.%, Sc: 0.2wt.%, Hf: 0.2wt.%, W: 0.4wt .%, the balance is iron. Alloy preparation method: Add the above-mentioned raw materials into an argon-protected induction furnace, and use a silicon carbide crucible; induction heating to 1500-1600 degrees to form an alloy solution, and use the electromagnetic stirring effect to fully stir for about 10 minutes; The alloy liquid is kept at 1500-1600 degrees for 10 minutes and then cast into the required round ingot. The obtained ingot is hot-rolled at 800 degrees, and the rolling reduction in each pass is 10-15%. After every two hot rollings, the intermediate annealing temperature is 900 degrees, and the temperature is kept for 1 hour. Finally, the material is rolled into a steel plate with a thickness of 40-60mm, and the ...
PUM
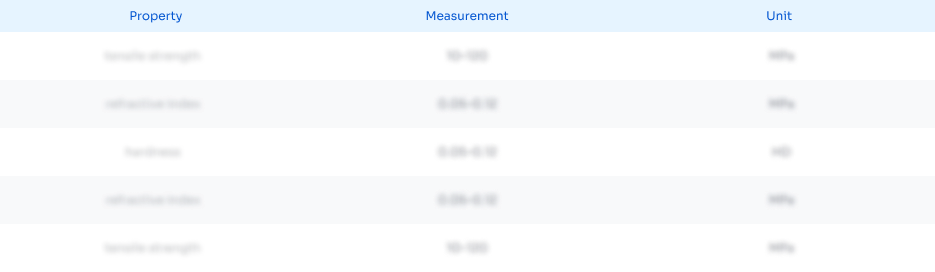
Abstract
Description
Claims
Application Information

- R&D Engineer
- R&D Manager
- IP Professional
- Industry Leading Data Capabilities
- Powerful AI technology
- Patent DNA Extraction
Browse by: Latest US Patents, China's latest patents, Technical Efficacy Thesaurus, Application Domain, Technology Topic, Popular Technical Reports.
© 2024 PatSnap. All rights reserved.Legal|Privacy policy|Modern Slavery Act Transparency Statement|Sitemap|About US| Contact US: help@patsnap.com