Adsorption reactor and method for separating high-boiling-point coagulable components from mixed gas
A mixed gas and reactor technology, applied in separation methods, chemical instruments and methods, gas treatment, etc., to achieve simple and convenient operation, increase adsorption efficiency and desorption efficiency, and small working volume
- Summary
- Abstract
- Description
- Claims
- Application Information
AI Technical Summary
Problems solved by technology
Method used
Image
Examples
Embodiment 1
[0079] One of the implementations of an adsorption reactor for separating high-boiling condensable components in a mixed gas of the present invention, such as Figure 1 to Figure 2 It shows that the adsorption reactor 1 includes a cylindrical shell 11 and a front vent 12 and a rear vent 13 at both ends of the shell 11. The shell 11 is provided with a microfiber fabric filler 14 and a compacting device. The filler 14 is filled in the casing 11; the pressing device is placed at one end of the casing, including a driving unit and a pressing plate 18, and the driving unit drives the pressing plate 18 to compress or loosen the microfiber filler 14. It should be understood that the front vents 12 and the rear vents 13 at both ends of the housing 11 can be symmetrically distributed, and can also be appropriately adjusted according to the actual situation. Two front vents and two rear vents can be provided respectively, and two front vents The vents are the gas inlet for the mixed gas...
Embodiment 2
[0088] One of the implementations of an adsorption reactor for separating high-boiling condensable components in a mixed gas of the present invention, such as Figure 1 to Figure 2 express. The main technical solution of this embodiment 2 is basically the same as that of embodiment 1, and the features not explained in this embodiment 2 are explained in embodiment 1, and will not be repeated here. The difference between this embodiment and Embodiment 1 is that one end of the pressing plate 18 is provided with a plurality of pressing sheets which are flexibly connected and distributed in the filler of polyester microfiber fabric, and the diameter of the pressing sheets is smaller than that of the pressing plate 18 . Each compression sheet is connected with the pressing plate 18 through a belt connection or a chain connection, and the polyester microfiber fabric filler is filled between the compression sheets. When the pressing plate 18 compresses the polyester microfiber fabric ...
Embodiment 3
[0091] One of the implementations of an adsorption reactor for separating high-boiling condensable components in a mixed gas of the present invention, such as Figure 1 to Figure 2 express. The main technical solution of this embodiment 3 is basically the same as that of embodiment 1 or embodiment 2, and the features not explained in this embodiment 3 are explained in embodiment 1 or embodiment 2, and will not be repeated here. The difference between this embodiment and embodiment 1 or embodiment 2 is: because the mixed gas contains acid corrosive gas SO 2 , high concentration Br 2 (Br 2 The flue gas is a high boiling point condensable component), and the inner wall of the housing 11 is lined with a polytetrafluoroethylene anti-corrosion layer.
[0092] Specifically, the height / diameter ratio of the adsorption reactor is 10. Specifically, the driving unit is configured as a motor rack driving device. The motor is fixed at one end of the adsorption reactor, and the linear ...
PUM
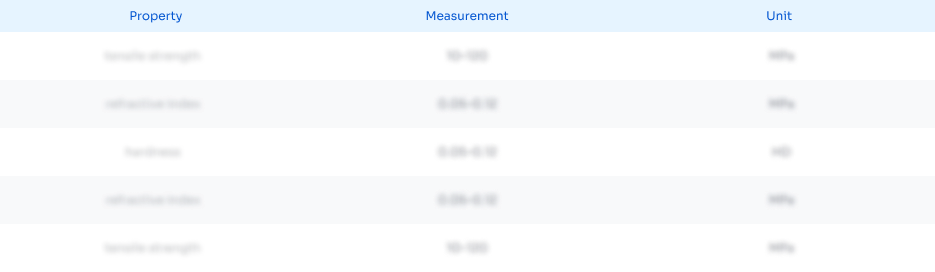
Abstract
Description
Claims
Application Information

- R&D
- Intellectual Property
- Life Sciences
- Materials
- Tech Scout
- Unparalleled Data Quality
- Higher Quality Content
- 60% Fewer Hallucinations
Browse by: Latest US Patents, China's latest patents, Technical Efficacy Thesaurus, Application Domain, Technology Topic, Popular Technical Reports.
© 2025 PatSnap. All rights reserved.Legal|Privacy policy|Modern Slavery Act Transparency Statement|Sitemap|About US| Contact US: help@patsnap.com