Graphene production process
A production process, graphene technology, applied in the field of graphene production process, can solve the problems of poor vibration effect, low efficiency of raw material paving, no effective measures to prevent feeding blockage and local accumulation, etc., to achieve the effect of avoiding blockage
- Summary
- Abstract
- Description
- Claims
- Application Information
AI Technical Summary
Problems solved by technology
Method used
Image
Examples
Embodiment Construction
[0030] In order to make the technical means, creative features, goals and effects achieved by the present invention easy to understand, the present invention will be further described below in conjunction with specific embodiments.
[0031] Such as Figure 1 to Figure 5 Shown, a kind of graphene production technique of the present invention, this technique comprises the following steps:
[0032] Step 1: Put the graphite block into the crusher and break it into graphite particles;
[0033] Step 2: mixing potassium permanganate, concentrated sulfuric acid and graphite particles in step 1 to obtain graphite oxide flakes;
[0034]Step 3: putting the graphite oxide flakes in step 2 into the reactor to obtain graphene oxide;
[0035] Step 4: passing the graphene oxide in step 3 into a hydrazine hydrate solution to obtain graphene;
[0036] Step five: the graphene in step four is placed in a vacuum drying oven to dry;
[0037] Wherein, the reaction kettle includes a box body 1, a...
PUM
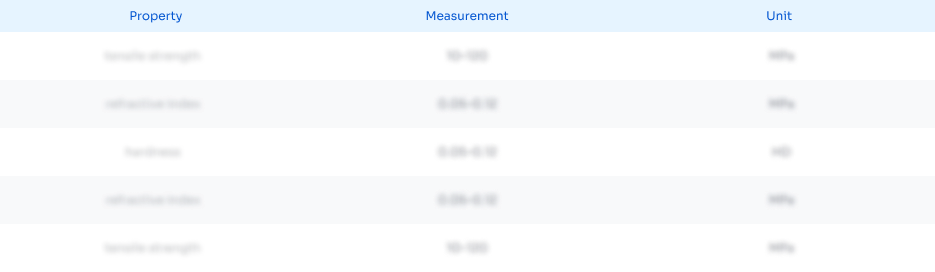
Abstract
Description
Claims
Application Information

- R&D Engineer
- R&D Manager
- IP Professional
- Industry Leading Data Capabilities
- Powerful AI technology
- Patent DNA Extraction
Browse by: Latest US Patents, China's latest patents, Technical Efficacy Thesaurus, Application Domain, Technology Topic, Popular Technical Reports.
© 2024 PatSnap. All rights reserved.Legal|Privacy policy|Modern Slavery Act Transparency Statement|Sitemap|About US| Contact US: help@patsnap.com