Friction-stir welding device applied to numerically-controlled machine tool
A technology of CNC machine tools and friction devices, which is applied in welding equipment, non-electric welding equipment, metal processing equipment, etc., can solve problems such as single shape or specified shape weldments, and achieve strong versatility, strong practicability, and excellent weld performance Effect
- Summary
- Abstract
- Description
- Claims
- Application Information
AI Technical Summary
Problems solved by technology
Method used
Image
Examples
Embodiment Construction
[0026] The detailed content of the present invention and its specific implementation will be further described below in conjunction with the accompanying drawings.
[0027] see Figure 1 to Figure 9 As shown, the electromagnetic assisted friction stir device applied to numerically controlled machine tools of the present invention includes a welding working module, a clamping module, a positioning module, a driving module, a direct current loading module and a magnetic field loading module. The device is characterized in that the positioning module is installed on the clamp The tightening module and the clamping module play the role of positioning and clamping together; the welding working module is installed on the CNC machine tool, and is driven by the spindle of the CNC machine tool to realize rotation and linear motion, and the driving module drives the clamping module to realize the vacuum fixture welding table 19 There is always a rotary motion with an inclination angle o...
PUM
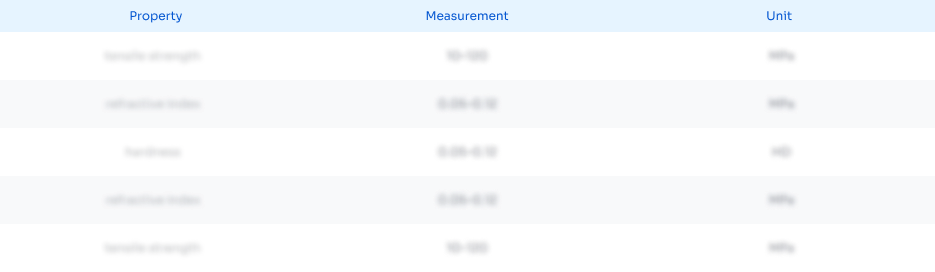
Abstract
Description
Claims
Application Information

- R&D Engineer
- R&D Manager
- IP Professional
- Industry Leading Data Capabilities
- Powerful AI technology
- Patent DNA Extraction
Browse by: Latest US Patents, China's latest patents, Technical Efficacy Thesaurus, Application Domain, Technology Topic, Popular Technical Reports.
© 2024 PatSnap. All rights reserved.Legal|Privacy policy|Modern Slavery Act Transparency Statement|Sitemap|About US| Contact US: help@patsnap.com