Reactor for the recovery of by-product acetonitrile in the production process of acrylonitrile
A production process and reactor technology, applied in chemical/physical process, chemical/physical/physicochemical process, product, etc., can solve problems such as explosive gas leakage, agitator blade falling off, temperature fluctuation increase, etc. Achieve the effect of efficient and uniform mixing, large mixing capacity and low operating pressure
- Summary
- Abstract
- Description
- Claims
- Application Information
AI Technical Summary
Problems solved by technology
Method used
Image
Examples
Embodiment Construction
[0025] Embodiments of the present invention will be described in detail below in conjunction with the accompanying drawings.
[0026] Such as figure 1 As shown, the present invention provides a reactor for the recovery of by-product acetonitrile in the production process of acrylonitrile. The reactor includes a cylinder body 5 , a left head 1 and a right head 10 . Further, a first circulating mixed reaction liquid inlet 2 , a feed pipe 3 and a second circulating mixed reaction liquid inlet 6 are provided on the outer wall of the cylinder 5 along the centerline of the longitudinal vertical cross section of the reactor. In addition, the inlet 6 of the second circulating mixed reaction liquid is connected with an upper two-way injector b and a lower two-way injector c, and the inlet 2 of the first circulating mixed reaction liquid is connected with a one-way injector a.
[0027] In the above embodiment, the circulating mixed reaction liquid is ejected from injectors a, b and c ...
PUM
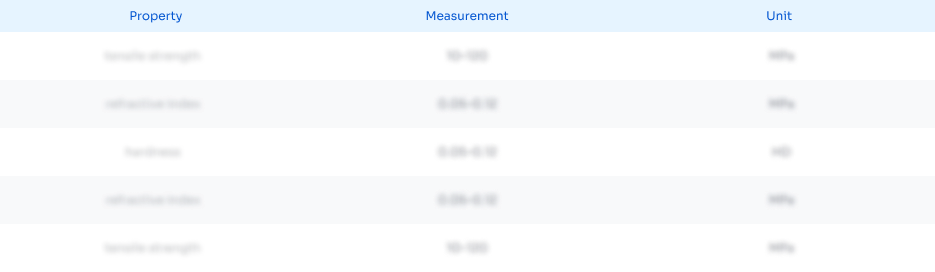
Abstract
Description
Claims
Application Information

- Generate Ideas
- Intellectual Property
- Life Sciences
- Materials
- Tech Scout
- Unparalleled Data Quality
- Higher Quality Content
- 60% Fewer Hallucinations
Browse by: Latest US Patents, China's latest patents, Technical Efficacy Thesaurus, Application Domain, Technology Topic, Popular Technical Reports.
© 2025 PatSnap. All rights reserved.Legal|Privacy policy|Modern Slavery Act Transparency Statement|Sitemap|About US| Contact US: help@patsnap.com