Self-lubricating hot-forging die based on Sialon ceramic and manufacturing method thereof
A hot forging die, self-lubricating technology, applied in metal processing equipment, transportation and packaging, etc., can solve the problems of lubricating oil pollution, friction and wear of hot forging die, etc., and achieve the effect of avoiding environmental pollution problems.
- Summary
- Abstract
- Description
- Claims
- Application Information
AI Technical Summary
Problems solved by technology
Method used
Image
Examples
preparation example Construction
[0039] refer to Figure 4 , a kind of preparation method of self-lubricating hot forging die based on Sialon ceramics, comprises the following steps:
[0040] Step S10, weighing an appropriate amount of NiCr metal powder, Sialon ceramic powder, CaF 2 After powder and stearic acid granules, put the weighed powder into a metal tank, add stainless steel balls, vacuumize and fill with nitrogen for protection, and use a ball mill to mix the powder by ball milling;
[0041] Step S20, the mixed powder is pressed and formed by a mold, and placed in a vacuum tube sintering furnace for sintering to form;
[0042] In step S30, after the sintered sample is polished, it is prepared into an insert and applied in a hot forging mold.
[0043] In step S10, the ball mill mixes the powder for 4-6 hours. If the ball milling time is too short, the material will be mixed unevenly, if the time is too long, cold welding will occur between the powders, and the powder particles will become thicker. ...
Embodiment example 1
[0051] A NiCr-Sialon-CaF 2 Self-lubricating mold material, prepared by the following method.
[0052] 1. Configure NiCr-Sialon-CaF 2 Powder: Take 80 parts of Ni80Cr20 powder, 10 parts of Sialon powder, CaF 2 10 parts of powder, 1.5 parts of stearic acid as a forming agent; put it in a metal tank, vacuumize and fill it with nitrogen, and mix it by ball milling for 5 hours, the ratio of ball to material is 1:6, and the speed is 200r / min;
[0053] 2. The powder mixed with the ball mill is sieved, the pore size of the screen is 200 mesh, the prepared powder is taken and pressed in the mold, the pressure is 22Mpa, and the holding time is 1min;
[0054] 3. The pressed and formed pattern is placed in a crucible, heated to 1200 degrees Celsius in a vacuum tube furnace, and kept for two hours;
[0055] 4. The heating program of the vacuum tube furnace: After 1 hour, heat to 400°C; keep at 400°C for 30 minutes; then heat to 1200°C after two hours, keep at 1200°C for 2 hours; Cool to...
PUM
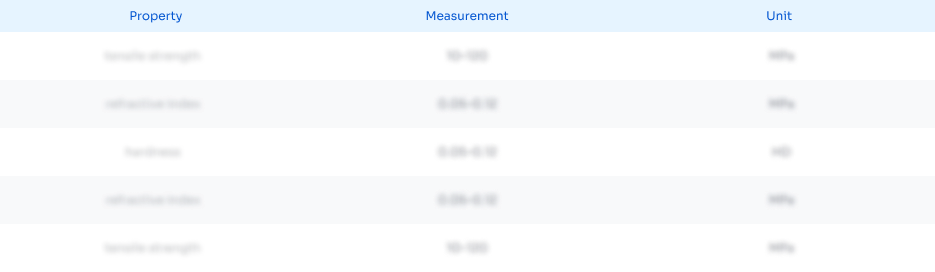
Abstract
Description
Claims
Application Information

- R&D
- Intellectual Property
- Life Sciences
- Materials
- Tech Scout
- Unparalleled Data Quality
- Higher Quality Content
- 60% Fewer Hallucinations
Browse by: Latest US Patents, China's latest patents, Technical Efficacy Thesaurus, Application Domain, Technology Topic, Popular Technical Reports.
© 2025 PatSnap. All rights reserved.Legal|Privacy policy|Modern Slavery Act Transparency Statement|Sitemap|About US| Contact US: help@patsnap.com