Method for rapidly stripping waste liquid crystal display polarizer
A liquid crystal display and polarizer technology, applied in chemical instruments and methods, solid waste removal, transportation and packaging, etc., can solve the problems of loss of use value, large amount of acetone, complicated steps, etc., to avoid toxic side effects and equipment requirements Low, the effect of increasing the peeling rate
- Summary
- Abstract
- Description
- Claims
- Application Information
AI Technical Summary
Problems solved by technology
Method used
Image
Examples
Embodiment 1
[0031] This embodiment provides a method for quickly peeling off the waste liquid crystal display polarizer:
[0032] 1. Use a flat screwdriver to pry open the metal frame of the waste liquid crystal display along the seam, take out the backlight module for recycling, and the well-preserved film can be reused, and the LCD screen, plastic frame, and metal frame are recycled separately.
[0033] 2. Use a knife to cut along the corner of the LCD screen to separate the upper and lower glass panels.
[0034] 3. Immerse the glass panel in 80°C water for 20 minutes. When the color of the polarizer is found to change from dark to light, take it out, and peel off the polarizer film layer composed of PET film, triacetate cellulose film and polyvinyl alcohol film in the polarizer. The peeled part will return to its original shape after the surface is naturally air-dried.
[0035] 4. Immerse the upper glass substrate with only the triacetate cellulose film in acetone for 15 minutes and t...
Embodiment 2
[0039] This embodiment provides a method for quickly peeling off the waste liquid crystal display polarizer:
[0040] 1. Use a flat screwdriver to pry open the metal frame of the waste liquid crystal display along the seam, take out the backlight module for recycling, and the well-preserved film can be reused, and the LCD screen, plastic frame, and metal frame are recycled separately.
[0041] 2. Use a knife to cut along the corner of the LCD screen to separate the upper and lower glass panels.
[0042] 3. Immerse the glass panel in 100°C water for 5 minutes. When the color of the polarizer is found to change from dark to light, take it out, and peel off the combined film layer of PET film, triacetate cellulose film and polyvinyl alcohol film in the polarizer. The peeled part will return to its original shape after the surface is naturally air-dried.
[0043] 4. Immerse the upper glass substrate with only the triacetate cellulose film in acetone for 15 minutes and the lower g...
Embodiment 3
[0046] This embodiment provides a method for quickly peeling off the waste liquid crystal display polarizer:
[0047]1. Use a flat screwdriver to pry open the metal frame of the waste liquid crystal display along the seam, take out the backlight module for recycling, and the well-preserved film can be reused, and the LCD screen, plastic frame, and metal frame are recycled separately.
[0048] 2. Use a knife to cut along the corner of the LCD screen to separate the upper and lower glass panels.
[0049] 3. Immerse the glass panel in 90°C water for 10 minutes. When the color of the polarizer is found to change from dark to light, take it out, and peel off the combined film layer of PET film, triacetate cellulose film and polyvinyl alcohol film in the polarizer. The peeled part will return to its original shape after the surface is naturally air-dried.
[0050] 4. Immerse the upper and lower glass substrates with only the triacetate cellulose film in acetone for 30 minutes to ma...
PUM
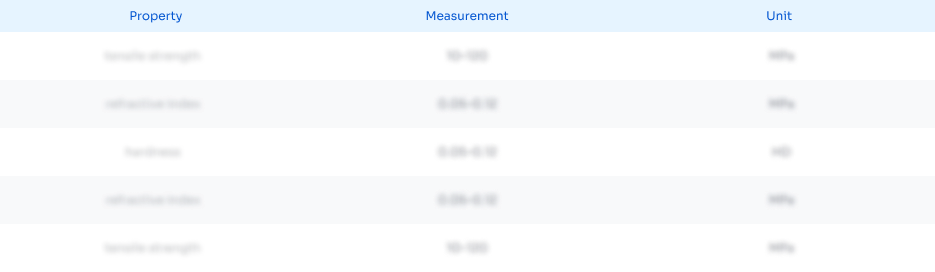
Abstract
Description
Claims
Application Information

- Generate Ideas
- Intellectual Property
- Life Sciences
- Materials
- Tech Scout
- Unparalleled Data Quality
- Higher Quality Content
- 60% Fewer Hallucinations
Browse by: Latest US Patents, China's latest patents, Technical Efficacy Thesaurus, Application Domain, Technology Topic, Popular Technical Reports.
© 2025 PatSnap. All rights reserved.Legal|Privacy policy|Modern Slavery Act Transparency Statement|Sitemap|About US| Contact US: help@patsnap.com