Glass yarn glue-dipping method
A technology of glass yarn and rubber dipping, which is applied in the field of hollow reactor production, can solve the problems of waste of raw materials, product quality, slow speed of glass yarn, inconvenience for users, etc., and achieves short preparation time, reduced burden and cost, and smooth yarn output Effect
- Summary
- Abstract
- Description
- Claims
- Application Information
AI Technical Summary
Problems solved by technology
Method used
Image
Examples
Embodiment Construction
[0023] The present invention can realize infiltration of glass yarn based on vacuum prepreg equipment, see figure 1 and figure 2 , a glass yarn dipping process, comprising the following steps: step 1, place the rolled glass yarn 1 in a vacuum box 2, the vacuum box 2 is connected with a vacuum pump 3 and a pressure relief valve 4, turn on the vacuum pump 3, make the vacuum box 2 Form a vacuum environment; Step 2, flow the prepared mixture of epoxy resin and curing agent into the vacuum box 2, until the liquid level of the mixture exceeds a certain height of the highest surface of the glass yarn 1; Step 3, continue to the vacuum box 2. The mixed solution is degassed until no large amount of bubbles emerge from the mixed solution; in step 4, the pressure relief valve 4 is opened to allow the outside air to enter the vacuum box 2, and the mixed solution is affected by the unbalanced internal and external air pressure and penetrates into the glass yarn 1. The mixture is soaked in...
PUM
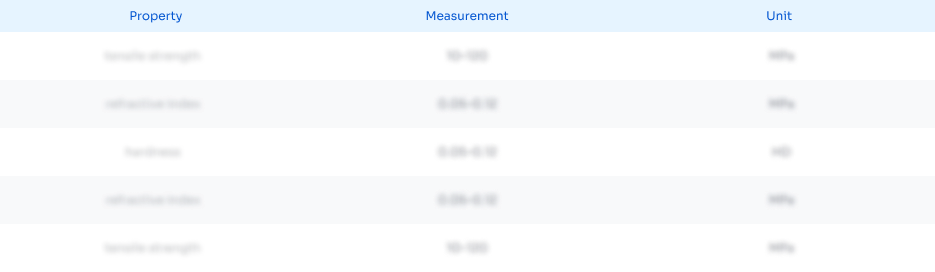
Abstract
Description
Claims
Application Information

- R&D
- Intellectual Property
- Life Sciences
- Materials
- Tech Scout
- Unparalleled Data Quality
- Higher Quality Content
- 60% Fewer Hallucinations
Browse by: Latest US Patents, China's latest patents, Technical Efficacy Thesaurus, Application Domain, Technology Topic, Popular Technical Reports.
© 2025 PatSnap. All rights reserved.Legal|Privacy policy|Modern Slavery Act Transparency Statement|Sitemap|About US| Contact US: help@patsnap.com