Thermoplastic resin film manufacturing method and cyclic olefin resin film
A technology of thermoplastic resin and manufacturing method, which is applied in the field of cyclic olefin resin film, can solve the problems of uneven and large optical film quality, light transmittance reduction, influence, etc., and achieves suppression of heat-degraded foreign matter and high light transmittance Effect
- Summary
- Abstract
- Description
- Claims
- Application Information
AI Technical Summary
Problems solved by technology
Method used
Image
Examples
Embodiment 1~ Embodiment 7
[0189] Cyclic olefin resin (ARTON (registered trademark) manufactured by JSR CORPORATION, specific gravity ρ: 1.08 (g / cm 3 ), glass transition temperature Tg: 138°C), by changing (changing the temperature of the extruder supply section A) the compression ratio, the supply section groove depth Hf, the barrel inner diameter D or Q of the extruder as shown in Table 1 / N, melt extrusion was carried out by adjusting so as to maintain the predetermined resin transfer efficiency in the supply section. In addition, the screw of the extruder is a full-flight type, and the screw flight angle is 17.7°.
Embodiment 8
[0191] In Example 1, melt extrusion was implemented in the same manner as in Example 1 except that the raw material resin was changed to polycarbonate.
Embodiment 1-a~ Embodiment 1-i
[0193] In Example 1, melt extrusion was carried out in the same manner as in Example 1, except that the oxygen concentration at the supply port of the extruder, the input resin temperature, the use of a vacuum hopper, and the screw or screw temperature were changed. In addition, the screw flight angle in the supply section of the double-flight type in Example 1-a to Example 1-i was 17.7°.
PUM
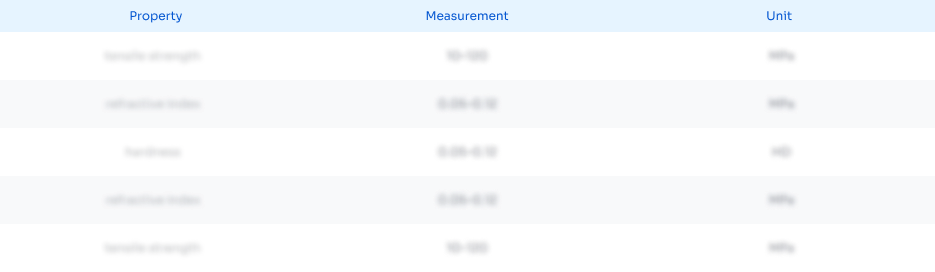
Abstract
Description
Claims
Application Information

- R&D
- Intellectual Property
- Life Sciences
- Materials
- Tech Scout
- Unparalleled Data Quality
- Higher Quality Content
- 60% Fewer Hallucinations
Browse by: Latest US Patents, China's latest patents, Technical Efficacy Thesaurus, Application Domain, Technology Topic, Popular Technical Reports.
© 2025 PatSnap. All rights reserved.Legal|Privacy policy|Modern Slavery Act Transparency Statement|Sitemap|About US| Contact US: help@patsnap.com