Textile knitting wool dyeing and drying equipment
A technology for drying equipment and wool, which is applied in the processing of textile material equipment configuration, textile and papermaking, and textile material processing.
- Summary
- Abstract
- Description
- Claims
- Application Information
AI Technical Summary
Problems solved by technology
Method used
Image
Examples
Embodiment 1
[0028] A kind of wool dyeing and drying equipment for textile, such as Figure 1-5 As shown, it includes a bottom plate 1, a fixed seat 2, a dye box 3, a valve 4, a feeding pipe 5, a first support plate 6, a connecting plate 7, a connecting block 8, a first electric wheel 9, a first set of wheels 10, Second support plate 11, L-shaped bar 12, second set of wheels 13, fixed rod 14, guide sleeve 15, guide rail 16, roller 17, first slide rail 18, first slider 19, mounting rod 20, second electric motor Wheel 21, turntable 22 and moving bar 23, bottom plate 1 left side is connected with fixed seat 2, fixed seat 2 upper end is connected with dye box 3, dye box 3 lower side right side is connected with feeding pipe 5, the upper side of feeding pipe 5 The valve 4 is connected, the upper right side of the bottom plate 1 is connected with the first supporting plate 6, the upper end of the first supporting plate 6 is connected with the connecting plate 7, the lower side of the connecting ...
Embodiment 2
[0030] A kind of wool dyeing and drying equipment for textile, such as Figure 1-5 As shown, it includes a bottom plate 1, a fixed seat 2, a dye box 3, a valve 4, a feeding pipe 5, a first support plate 6, a connecting plate 7, a connecting block 8, a first electric wheel 9, a first set of wheels 10, Second support plate 11, L-shaped bar 12, second set of wheels 13, fixed rod 14, guide sleeve 15, guide rail 16, roller 17, first slide rail 18, first slider 19, mounting rod 20, second electric motor Wheel 21, turntable 22 and moving bar 23, bottom plate 1 left side is connected with fixed seat 2, fixed seat 2 upper end is connected with dye box 3, dye box 3 lower side right side is connected with feeding pipe 5, the upper side of feeding pipe 5 The valve 4 is connected, the upper right side of the bottom plate 1 is connected with the first supporting plate 6, the upper end of the first supporting plate 6 is connected with the connecting plate 7, the lower side of the connecting ...
Embodiment 3
[0033] A kind of wool dyeing and drying equipment for textile, such as Figure 1-5 As shown, it includes a bottom plate 1, a fixed seat 2, a dye box 3, a valve 4, a feeding pipe 5, a first support plate 6, a connecting plate 7, a connecting block 8, a first electric wheel 9, a first set of wheels 10, Second support plate 11, L-shaped bar 12, second set of wheels 13, fixed rod 14, guide sleeve 15, guide rail 16, roller 17, first slide rail 18, first slider 19, mounting rod 20, second electric motor Wheel 21, turntable 22 and moving bar 23, bottom plate 1 left side is connected with fixed seat 2, fixed seat 2 upper end is connected with dye box 3, dye box 3 lower side right side is connected with feeding pipe 5, the upper side of feeding pipe 5 The valve 4 is connected, the upper right side of the bottom plate 1 is connected with the first supporting plate 6, the upper end of the first supporting plate 6 is connected with the connecting plate 7, the lower side of the connecting ...
PUM
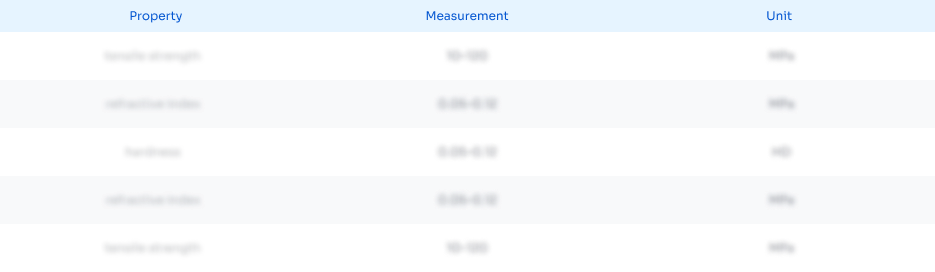
Abstract
Description
Claims
Application Information

- Generate Ideas
- Intellectual Property
- Life Sciences
- Materials
- Tech Scout
- Unparalleled Data Quality
- Higher Quality Content
- 60% Fewer Hallucinations
Browse by: Latest US Patents, China's latest patents, Technical Efficacy Thesaurus, Application Domain, Technology Topic, Popular Technical Reports.
© 2025 PatSnap. All rights reserved.Legal|Privacy policy|Modern Slavery Act Transparency Statement|Sitemap|About US| Contact US: help@patsnap.com