Self-adaptive control method for reinforcement learning of brush DC motor
A brushed DC motor, self-adaptive control technology, applied in the field of motors, can solve problems such as dead zone, crawling and low-speed instability
- Summary
- Abstract
- Description
- Claims
- Application Information
AI Technical Summary
Problems solved by technology
Method used
Image
Examples
Embodiment Construction
[0123] Through continuous research and practice, the inventors of the present invention found that the appropriate adaptive rate can estimate the friction torque and cogging torque parameters online, so as to achieve the purpose of accurately compensating the motor friction torque and cogging torque; The unknown disturbance estimation and compensation strategy can suppress the impact of unknown disturbances on the smoothness of the motor's steady-state operation, and this method can bring better speed tracking performance to the motor. Based on the mathematical model of the brushed DC motor, the invention designs an adaptive control method of the brushed DC motor based on reinforcement learning.
[0124] The steps of the present invention are:
[0125] (1) Establish the mathematical model of the brushed DC motor
[0126] figure 1 It is the schematic diagram of the brushed DC motor circuit. It can be seen that the equivalent circuit of the brushed DC motor is the series conne...
PUM
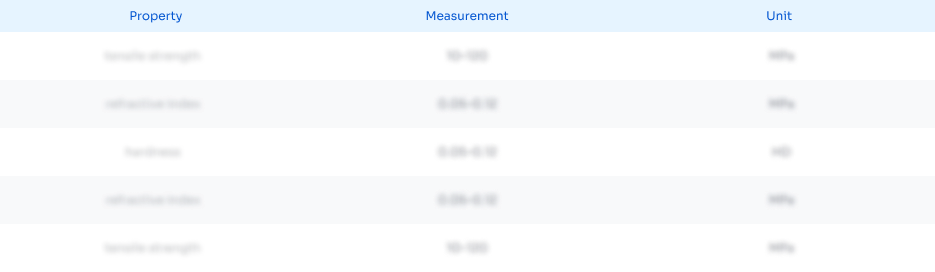
Abstract
Description
Claims
Application Information

- Generate Ideas
- Intellectual Property
- Life Sciences
- Materials
- Tech Scout
- Unparalleled Data Quality
- Higher Quality Content
- 60% Fewer Hallucinations
Browse by: Latest US Patents, China's latest patents, Technical Efficacy Thesaurus, Application Domain, Technology Topic, Popular Technical Reports.
© 2025 PatSnap. All rights reserved.Legal|Privacy policy|Modern Slavery Act Transparency Statement|Sitemap|About US| Contact US: help@patsnap.com