Heat treatment method for aluminum alloy forcing shaping and aluminum alloy section for aviation
A heat treatment method and aluminum alloy profile technology, which is applied in the field of aluminum alloy processing, can solve problems such as bending deformation, achieve good straightness, and solve the effect of bending deformation
- Summary
- Abstract
- Description
- Claims
- Application Information
AI Technical Summary
Problems solved by technology
Method used
Image
Examples
Embodiment 1
[0048] This embodiment provides a 2026 aluminum alloy product, which is made by adopting the following heat treatment method of forced shaping of aluminum alloy:
[0049] (1) Extrusion: Heat the aluminum alloy cast rod in a power frequency furnace at a heating temperature of 360°C, put the heated cast rod into an extrusion cylinder for extrusion treatment to obtain an extruded profile, and the exit speed of the extruded profile is 1.5m / min, the outlet temperature is 365°C.
[0050] (2) Quenching: the extruded profile is fixedly placed in the prefabricated aluminum alloy forced forming device 100, and enters the horizontal quenching furnace with the feeding basket for solid solution and quenching. The solid solution temperature is 495°C, and the holding time is 120min. The quenching transfer time is 15s, and the quenched profile is obtained.
[0051] The distance between the two single-piece fixtures 120 of the aluminum alloy forced shaping device 100 used in the quenching pr...
Embodiment 2
[0056] This embodiment provides a 2026 aluminum alloy product, which is made by adopting the following heat treatment method of forced shaping of aluminum alloy:
[0057] (1) Extrusion: Heat the aluminum alloy cast rod in a power frequency furnace at a heating temperature of 380°C, put the heated cast rod into an extrusion cylinder for extrusion treatment to obtain an extruded profile, and the exit speed of the extruded profile is 0.8m / min, the outlet temperature is 390°C.
[0058] (2) Quenching: the extruded profile is fixedly placed in the prefabricated aluminum alloy forced shaping device 100, and enters the horizontal quenching furnace with the feeding basket for solid solution and quenching. The solid solution temperature is 497°C, and the holding time is 150min. The quenching transfer time is 20s, and the quenched profile is obtained.
[0059] The distance between the two single-piece fixtures 120 of the aluminum alloy forced shaping device 100 used in the quenching pr...
Embodiment 3
[0064] This embodiment provides a 2024 aluminum alloy product, which is made by adopting the following heat treatment method for forced shaping of aluminum alloy:
[0065] (1) Extrusion: Heat the aluminum alloy cast rod in a power frequency furnace, the heating temperature is 370°C, put the heated cast rod into the extrusion cylinder for extrusion treatment to obtain an extruded profile, and the exit speed of the extruded profile is 1.5m / min, the outlet temperature is 380°C.
[0066] (2) Quenching: The extruded profile is fixedly placed in the prefabricated aluminum alloy forced shaping device 100, and enters the horizontal quenching furnace with the feeding basket for solid solution and quenching. The solid solution temperature is 494°C, and the holding time is 150min. The quenching transfer time is 15s, and the quenched profile is obtained.
[0067] The distance between the two single-piece fixtures 120 of the aluminum alloy forced shaping device 100 used in the quenching ...
PUM
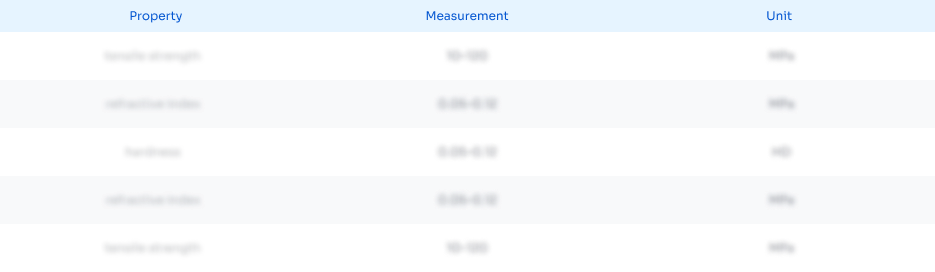
Abstract
Description
Claims
Application Information

- R&D
- Intellectual Property
- Life Sciences
- Materials
- Tech Scout
- Unparalleled Data Quality
- Higher Quality Content
- 60% Fewer Hallucinations
Browse by: Latest US Patents, China's latest patents, Technical Efficacy Thesaurus, Application Domain, Technology Topic, Popular Technical Reports.
© 2025 PatSnap. All rights reserved.Legal|Privacy policy|Modern Slavery Act Transparency Statement|Sitemap|About US| Contact US: help@patsnap.com