Thermoplastic elastomer
A technology of thermoplastic elastomers and parts by weight, applied in the field of thermoplastic elastomers, can solve the problems of difficult to achieve uniform mixing of raw materials, poor structural strength and elasticity of thermoplastic elastomer composite materials, poor compatibility, etc. The effect of slowing down aging and improving surface gloss
- Summary
- Abstract
- Description
- Claims
- Application Information
AI Technical Summary
Problems solved by technology
Method used
Image
Examples
Embodiment 1
[0029] Embodiment 1: A kind of thermoplastic elastomer, each component of raw material and weight parts are as shown in Table 1, and preparation method comprises the following steps:
[0030] Step 1, SEBS (hydrogenated styrene-butadiene block copolymer), SBS (styrene-butadiene-styrene block copolymer), PS (polystyrene), PP (polypropylene), carbon Black, nano-calcium carbonate, naphthenic oil 4010, antioxidant, stearic acid, silicone masterbatch, zinc stearate and dibutyl hydroxytoluene are put into a rotary mixer and mixed evenly to obtain a mixture;
[0031] In step 2, the mixture is added to a twin-screw extruder, the mixture is extruded through the extruder and injected into a mold, cooled, dried, and packaged to obtain a product made of thermoplastic elastomer.
Embodiment 2
[0032] Example 2: A thermoplastic elastomer, the difference from Example 1 is that the components and parts by weight of the raw materials are shown in Table 1.
Embodiment 3
[0033] Embodiment 3: A kind of thermoplastic elastomer, each component of raw material and weight parts are as shown in Table 1, and preparation method comprises the following steps:
[0034] Step 1, SEBS (hydrogenated styrene-butadiene block copolymer), SBS (styrene-butadiene-styrene block copolymer), PS (polystyrene), PP (polypropylene), carbon Black, nano-calcium carbonate, naphthenic oil 4010, antioxidant, stearic acid, silicone masterbatch and dibutyl hydroxytoluene are put into a rotary mixer and mixed evenly to obtain a mixture;
[0035]In step 2, the mixture is added to a twin-screw extruder, the mixture is extruded through the extruder and injected into a mold, cooled, dried, and packaged to obtain a product made of thermoplastic elastomer.
PUM
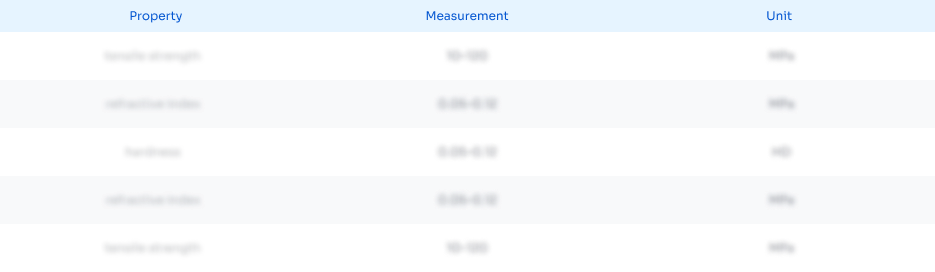
Abstract
Description
Claims
Application Information

- R&D
- Intellectual Property
- Life Sciences
- Materials
- Tech Scout
- Unparalleled Data Quality
- Higher Quality Content
- 60% Fewer Hallucinations
Browse by: Latest US Patents, China's latest patents, Technical Efficacy Thesaurus, Application Domain, Technology Topic, Popular Technical Reports.
© 2025 PatSnap. All rights reserved.Legal|Privacy policy|Modern Slavery Act Transparency Statement|Sitemap|About US| Contact US: help@patsnap.com