Preparation method of conductive polymer material
A conductive polymer and ultrasonic technology, applied in the field of polymer materials, can solve problems affecting material flexibility, physical and mechanical properties and processability, electrical conductivity and processing properties, mechanical properties, and poor compatibility of resins. Achieve the effect of enhancing mechanical properties, improving mechanical properties, and excellent thermal conductivity
- Summary
- Abstract
- Description
- Claims
- Application Information
AI Technical Summary
Problems solved by technology
Method used
Examples
Embodiment 1
[0024] A method for preparing a conductive polymer material, comprising the steps of:
[0025] a. Mix the waste steel slag and send it into a pulverizer for crushing, and then introduce it into a ball mill for ball milling for 1 hour, then use ultrasonic oscillation for 20 minutes, and then use alcohol to wash it for 3 times, and then put it in a drying oven and dry it at 90°C for 40 minutes to obtain a powder ;
[0026] b. Mix powder 1, polyaniline and organic resin into a kneader for melting, the melting temperature is 450°C, the time is 45min, and then keep warm to obtain mixture 1;
[0027] c. Mix calcium carbonate, carbon black and graphene oxide, add ethanol solution, stir for 40 minutes at a speed of 120r / min, disperse by ultrasonic oscillation for 10 minutes, add a pH value regulator, adjust the pH value to 5, and then place Heated in a water bath at 80°C for 3 hours, filtered, rinsed with distilled water 8 times, and dried in a vacuum oven for 40 minutes at a drying ...
Embodiment 2
[0037] A method for preparing a conductive polymer material, comprising the steps of:
[0038] a. Mix the waste steel slag and send it into a pulverizer for crushing, and then introduce it into a ball mill for ball milling for 1 hour, then use ultrasonic oscillation for 20 minutes, and then wash it with alcohol for 3 times, then put it in a drying oven and dry it at 80°C for 40 minutes to obtain a powder ;
[0039] b. Mix powder 1, polyaniline and organic resin into a kneader for smelting at a melting temperature of 360°C for 45 minutes, and then keep warm to obtain mixture 1;
[0040] c. Mix calcium carbonate, carbon black and graphene oxide, add ethanol solution, stir at a speed of 100r / min for 40min, then use ultrasonic oscillation to disperse for 10min, add a pH value regulator, adjust the pH value to 5, and then place Heated in a water bath at 60°C for 2 hours, filtered, rinsed with distilled water for 5 times, and then dried in a vacuum oven for 40 minutes at a drying t...
Embodiment 3
[0050] A method for preparing a conductive polymer material, comprising the steps of:
[0051] a. Mix the waste steel slag and send it into a pulverizer for crushing, then introduce it into a ball mill for ball milling for 2 hours, then use ultrasonic oscillation for 30 minutes, and then use alcohol to wash it for 5 times, then put it in a drying oven and dry it at 90°C for 50 minutes to obtain a powder ;
[0052] b. Mix powder 1, polyaniline and organic resin into a kneader for smelting at a melting temperature of 450°C for 55 minutes, and then keep warm to obtain mixture 1;
[0053] c. Mix calcium carbonate, carbon black and graphene oxide, add ethanol solution, stir at a speed of 120r / min for 60min, then use ultrasonic oscillation to disperse for 20min, add a pH value regulator, adjust the pH value to 6, and then place Heated in a water bath at 80°C for 3 hours, filtered, rinsed with distilled water 8 times, and dried in a vacuum oven for 50 minutes at a drying temperature...
PUM
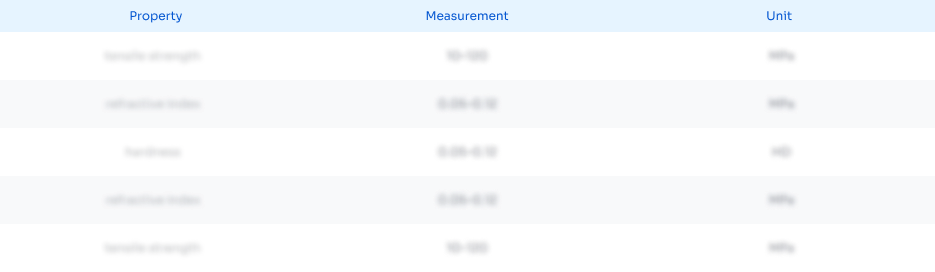
Abstract
Description
Claims
Application Information

- R&D Engineer
- R&D Manager
- IP Professional
- Industry Leading Data Capabilities
- Powerful AI technology
- Patent DNA Extraction
Browse by: Latest US Patents, China's latest patents, Technical Efficacy Thesaurus, Application Domain, Technology Topic, Popular Technical Reports.
© 2024 PatSnap. All rights reserved.Legal|Privacy policy|Modern Slavery Act Transparency Statement|Sitemap|About US| Contact US: help@patsnap.com