Waste organic solvent recycling method
An organic solvent and resource-based technology, which is applied in waste fuel, granular/powder fuel gasification, petroleum industry, etc., can solve the problems of unproduct processing, high processing cost, long time consumption, etc., and achieve efficient resource utilization and high efficiency. The effect of safe disposal and resolution of pollution risks
- Summary
- Abstract
- Description
- Claims
- Application Information
AI Technical Summary
Problems solved by technology
Method used
Image
Examples
Embodiment 1
[0075] This embodiment provides a method for resource utilization of waste organic solvents, the method comprising the following steps:
[0076] (1) Mix 19.92t of waste organic solvent produced by Hangzhou Chuanhua Fine Chemical Co., Ltd. with 19.92t of slag washing water and 0.30t of sodium naphthalenesulfonate, the mass ratio of which is 100:100:1.5, and use sulfuric acid solution to adjust the pH value of the mixture For 6.0, prepare the pretreatment solution;
[0077] (2) Mix the pretreatment liquid obtained in step (1) with 26.02t of coal evenly, the mass ratio of waste organic solvent to coal is 100:130.6, and use ball milling to prepare a solid content of 39.32wt% and a viscosity of 630mPa·s coal water slurry;
[0078] (3) spray the coal-water slurry prepared in step (2) into the gasification furnace with a special nozzle, and carry out the gasification reaction for 15 seconds at a temperature of 1450° C. and a pressure of 0.5 MPa in an oxygen-containing atmosphere con...
Embodiment 2
[0083] This embodiment provides a method for resource utilization of waste organic solvents, the method comprising the following steps:
[0084] (1) Mix 5.4t of waste organic solvent produced by Hyosung Chemical Fiber (Jiaxing) with 2.7t of slag flushing water and 0.16t of potassium lignosulfonate, the mass ratio of which is 100:100:3.0, and adjust with sodium hydroxide solution The pH value of the mixed solution is 7.0, and the pretreatment solution is prepared
[0085] (2) Mix the pretreatment liquid obtained in step (1) with 6.28 t of coke evenly, the mass ratio of waste organic solvent to coke is 100:116.3, adopt ball milling treatment, and prepare solid content is 43.2%, viscosity is 740mPa·s CWS;
[0086] (3) Spray the coal-water slurry prepared in step (2) into the gasification furnace with a special nozzle, and carry out the gasification reaction at 1700° C. and a pressure of 1.5 MPa for 2 seconds in an oxygen-containing atmosphere containing 99.7% oxygen, Obtain gas...
Embodiment 3
[0091] This embodiment provides a method for resource utilization of waste organic solvents, the method comprising the following steps:
[0092] (1) Mix 5.0t of organic solvent recovery waste liquid produced by Prodbon Pharmaceuticals with 12.5t of slag washing water and 0.25t of sodium sulfonated humate evenly, with a mass ratio of 100:250:5.0, and adjust with hydrochloric acid solution The pH value of the mixed solution is 5.0, and the pretreatment solution is prepared;
[0093] (2) Mix the pretreatment solution obtained in step (1) with 7.9t of activated carbon evenly, the mass ratio of waste organic solvent to activated carbon is 100:158, and adopt ball milling to prepare a solid content of 30.8wt% and a viscosity of 416mPa·s coal water slurry;
[0094] (3) Spray the coal-water slurry prepared in step (2) into the gasification furnace with a special nozzle, and carry out the gasification reaction for 8 seconds at a temperature of 1100° C. and a pressure of 4.0 MPa in an o...
PUM
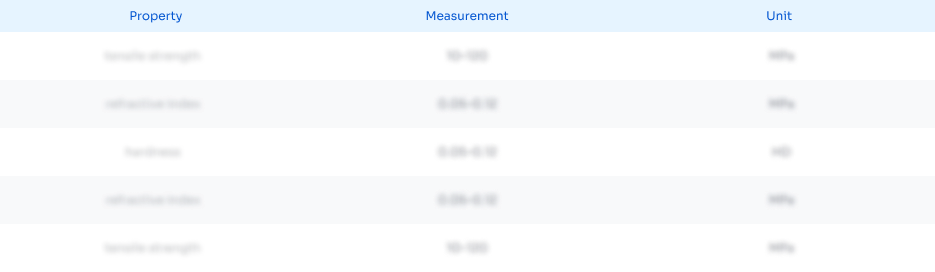
Abstract
Description
Claims
Application Information

- R&D
- Intellectual Property
- Life Sciences
- Materials
- Tech Scout
- Unparalleled Data Quality
- Higher Quality Content
- 60% Fewer Hallucinations
Browse by: Latest US Patents, China's latest patents, Technical Efficacy Thesaurus, Application Domain, Technology Topic, Popular Technical Reports.
© 2025 PatSnap. All rights reserved.Legal|Privacy policy|Modern Slavery Act Transparency Statement|Sitemap|About US| Contact US: help@patsnap.com