Preparation method of cyclic trimethylolpropane formaldehyde
A trimethylolpropane formal and cyclic technology, which is applied in the field of preparation of cyclic trimethylolpropane formal, can solve the problems of unsuitability for large-scale industrial production, cumbersome process, poor product quality, etc., and achieve reaction The effect of sufficient heat utilization, economical process and short reaction time
- Summary
- Abstract
- Description
- Claims
- Application Information
AI Technical Summary
Problems solved by technology
Method used
Image
Examples
Embodiment 1
[0023] Add 1340g of trimethylolpropane and 300g of paraformaldehyde into a stirred tank reactor, add 400g of toluene as a solvent, heat to 100°C, rotate at 22r / min, add 10g of sulfuric acid as a catalyst, and add 5g of ZSM -5 is auxiliary agent. After reaction for about 2h, low-pressure evaporation is carried out at an absolute pressure of 5KPa. After evaporation, the solution in the kettle is filtered, after removing the auxiliary agent and other solid substances, it enters the distillation tower for low-pressure rectification, the pressure is about 3KPa , The reflux ratio is 1:6, and the top of the tower is CTF product. The product CTF yield is 98%, the product purity is 98.8%, the APHA color number is 10, the sodium content is 11 ppm, and the water content is 0.2%.
Embodiment 2
[0025] Add 1340g of trimethylolpropane and 811g of formaldehyde solution into a stirred tank reactor, add 200g of ethanol as solvent, heat to 85°C, rotate at 18r / min, add 12g of ammonium bisulfate as a catalyst, and add 8g of MCM-41 is an auxiliary agent. It is reacted while vacuuming at an absolute pressure of 7KPa. After reacting for about 4h, the solution in the kettle is filtered to remove the auxiliary agent and other solid materials, and then enter the rectification tower for low-pressure rectification, the pressure is about 5KPa , Reflux ratio is 1:5, and the top of the tower is CTF product. The CTF yield of the product is 97.8%, the product purity is 98.5%, the APHA color number is 15, the sodium content is 10 ppm, and the water content is 0.3%.
Embodiment 3
[0027] Add 670Kg trimethylolpropane and 406Kg formaldehyde solution into a stirred reactor, heat to 95°C, rotate at 12r / min, add 5Kg sodium hydrogen sulfate as a catalyst, and react while vacuuming at an absolute pressure of 6KPa. After about 3h, filter the solution in the kettle to remove solid matter, then enter the rectification tower for low-pressure rectification, the pressure is about 4KPa, the reflux ratio is 1:5, and the top of the tower is the CTF product. The product CTF yield is 99.2%, the product purity is 99%, the APHA color number is 10, the sodium content is 12 ppm, and the water content is 0.12%.
PUM
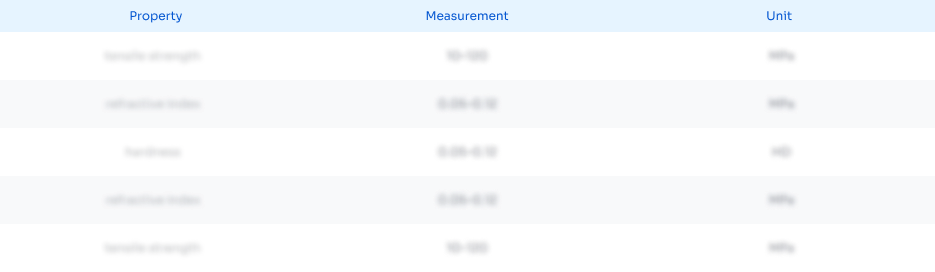
Abstract
Description
Claims
Application Information

- R&D
- Intellectual Property
- Life Sciences
- Materials
- Tech Scout
- Unparalleled Data Quality
- Higher Quality Content
- 60% Fewer Hallucinations
Browse by: Latest US Patents, China's latest patents, Technical Efficacy Thesaurus, Application Domain, Technology Topic, Popular Technical Reports.
© 2025 PatSnap. All rights reserved.Legal|Privacy policy|Modern Slavery Act Transparency Statement|Sitemap|About US| Contact US: help@patsnap.com