Peeling member and peeling device
一种构件、剥离片的技术,应用在仪器、应用电荷图形的电记录工艺的设备、光学等方向,能够解决无法得到图像、磨损、纸张易受到污染等问题,达到剥离性优异的效果
- Summary
- Abstract
- Description
- Claims
- Application Information
AI Technical Summary
Problems solved by technology
Method used
Image
Examples
Embodiment 1
[0060] After a stainless steel (SUS304CSP) coil with a thickness of 1.5 mm was processed into a predetermined size using a progressive stamping die, the tip portion was tapered by machining to manufacture a peeling member. based on Figure 8 The manufacturing process will be described. Figure 8 It is a schematic diagram of the manufacturing process. (A) to (F) are schematic processing procedures. First, the outer dimensions of the peeling sheet are punched out of the steel plate 20 shown in (A) with a punching die, and then, the concave portion 3c is formed by drawing shown in (B). Next, in (C), the bolt hole 3d for bolt fixing is punched out with a press die, and in (D), the drawn portion is cut into a predetermined size. Then, in (E), the peeling sheet 10' before forming a cone is punched out from the steel plate 20. Finally, in (F), the side opposite to the drawing portion opposite to the paper feed is cut into a tapered shape by machining, and then ground to obtain a ...
Embodiment 2
[0064] A stainless steel (SUS304CSP) coil with a thickness of 1.5 mm was processed to a predetermined size using a progressive die in the same manner as in Example 1, and then the thickness of the tip portion was processed to 0.3 mm by machining to manufacture a release member. The punching process using the stamping die is Figure 8 The processing sequence of (A) to (E), but after the peeling sheet 10' is punched out from the steel plate 20 after being processed by a stamping die, the tapered front end is cut in the longitudinal direction by stamping to improve the accuracy of straightness , the above-mentioned tapered tip is at Figure 8 In (F), the peeling sheet 10 having the peeling portion 2 and the support portion 3 is obtained by grinding the side opposite to the drawing portion opposite to the paper feeding into a tapered shape by machining. The thickness of the leading end portion of the release sheet 10 was 0.3 mm, and the width of the release portion of the release...
PUM
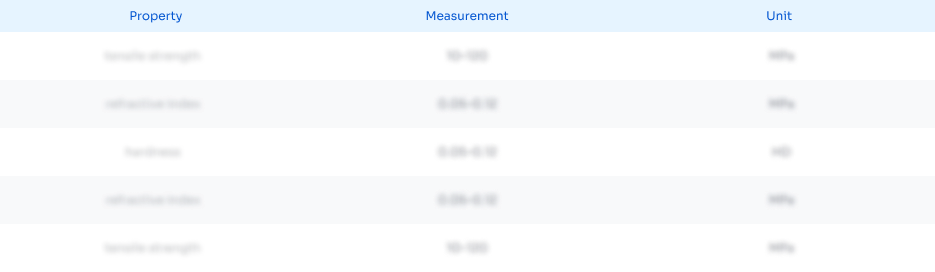
Abstract
Description
Claims
Application Information

- R&D
- Intellectual Property
- Life Sciences
- Materials
- Tech Scout
- Unparalleled Data Quality
- Higher Quality Content
- 60% Fewer Hallucinations
Browse by: Latest US Patents, China's latest patents, Technical Efficacy Thesaurus, Application Domain, Technology Topic, Popular Technical Reports.
© 2025 PatSnap. All rights reserved.Legal|Privacy policy|Modern Slavery Act Transparency Statement|Sitemap|About US| Contact US: help@patsnap.com