Spherical composite film digital paper for thermal sublimation transfer printing
A composite film and thermal sublimation technology, used in papermaking, paper, paper coatings, etc., can solve the problems of low coating yield and complex coating process, achieve high transfer efficiency, improve drying speed, and good ink absorption speed. Effect
- Summary
- Abstract
- Description
- Claims
- Application Information
AI Technical Summary
Problems solved by technology
Method used
Image
Examples
Embodiment 1
[0043] Spherical composite film transfer digital paper, such as Figure 1-4 As shown, it includes substrate paper 1, spherical composite film 2 and surface channel layer 3 from bottom to top. The spherical composite film 2 includes a spherical structure 21 and a resin structure 22. Microchannels 23 are provided on the spherical structure 21 .
[0044] The spherical composite membrane 2 is an interpenetrating network composite membrane composed of hydrophilic network resin and porous inorganic matter. The spherical composite membrane 2 is calculated by mass percentage, and the components and contents are as follows:
[0045] Hydrophilic network resin 11%;
[0046] Porous inorganic matter 89%;
[0047] Wherein, the hydrophilic network resin is composed of 40% by mass of acrylic resin composition and 32% by mass of sodium carboxymethyl cellulose and 23% by mass of cationic polyacrylamide through 5% by mass. Interpenetrating network resin formed by crosslinking polyisocyanate. ...
Embodiment 2
[0061] Spherical composite film transfer digital paper, such as Figure 1-4 As shown, it includes substrate paper 1, spherical composite film 2 and surface channel layer 3 from bottom to top. The spherical composite film 2 includes a spherical structure 21 and a resin structure 22. Microchannels 23 are provided on the spherical structure 21 .
[0062] The spherical composite membrane 2 is an interpenetrating network composite membrane composed of hydrophilic network resin and porous inorganic matter. The spherical composite membrane 2 is calculated by mass percentage, and the components and contents are as follows:
[0063] Hydrophilic network resin 20%;
[0064] Porous inorganic matter 80%;
[0065] Wherein, the hydrophilic network resin is composed of 33% by mass of acrylic resin composition and 40% by mass of sodium carboxymethylcellulose and 23% by mass of cationic polyacrylamide, respectively, and 4% by mass. Interpenetrating network resin formed by crosslinking polyis...
Embodiment 3
[0077] Spherical composite film transfer digital paper, such as Figure 1-4 As shown, it includes substrate paper 1, spherical composite film 2 and surface channel layer 3 from bottom to top. The spherical composite film 2 includes a spherical structure 21 and a resin structure 22. Microchannels 23 are provided on the spherical structure 21 .
[0078] The spherical composite membrane 2 is an interpenetrating network composite membrane composed of hydrophilic network resin and porous inorganic matter. The spherical composite membrane 2 is calculated by mass percentage, and the components and contents are as follows:
[0079] Hydrophilic network resin 25%;
[0080] Porous inorganic matter 75%;
[0081] Wherein, the hydrophilic network resin is composed of 30% by mass of acrylic resin composition and 38% by mass of sodium carboxymethyl cellulose and 25% by mass of cationic polyacrylamide through 7% by mass Interpenetrating network resin formed by crosslinking polyisocyanate. ...
PUM
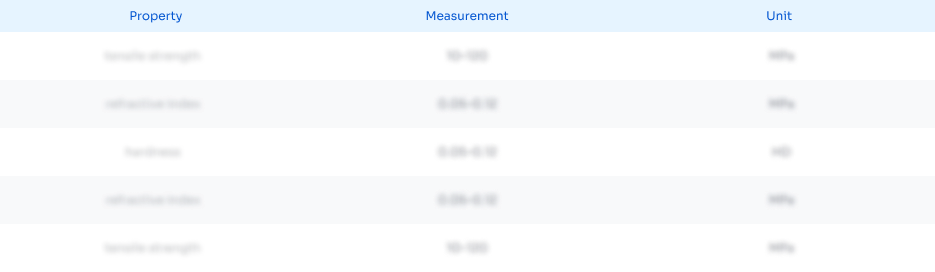
Abstract
Description
Claims
Application Information

- R&D Engineer
- R&D Manager
- IP Professional
- Industry Leading Data Capabilities
- Powerful AI technology
- Patent DNA Extraction
Browse by: Latest US Patents, China's latest patents, Technical Efficacy Thesaurus, Application Domain, Technology Topic, Popular Technical Reports.
© 2024 PatSnap. All rights reserved.Legal|Privacy policy|Modern Slavery Act Transparency Statement|Sitemap|About US| Contact US: help@patsnap.com