Method for automatically detecting and recognizing bridge cracks based on computer vision
A computer vision and automatic monitoring technology, applied in the testing, calculation, elasticity testing of machine/structural components, etc., can solve the problems of high cost, real crack identification interference, small fatigue crack size, etc., to improve efficiency and reduce Human participation, improve the effect of automation
- Summary
- Abstract
- Description
- Claims
- Application Information
AI Technical Summary
Problems solved by technology
Method used
Image
Examples
Embodiment 1
[0035] Such as figure 1 As shown, an automatic monitoring and identification method for bridge cracks based on computer vision, based on the implementation in the MATLAB environment:
[0036] The first step is to make the training set: the original input image is cut into a set of sub-units of 64×64×3, and a certain proportion of samples are randomly selected from them. Labeling, where the number 1 represents the crack unit, 2 represents the handwriting unit, and 3 represents the background unit. After completion, the newly added subunit set will be integrated into the original training set, and each subunit corresponds to the corresponding label. Considering the influence of the unbalanced sample size of the three types of subunits, display the number of the three subunits at this time, and take the number of subunits with the least number as the benchmark, randomly select the same number of samples from the remaining two types of subunit samples, and then, Rotate each subun...
PUM
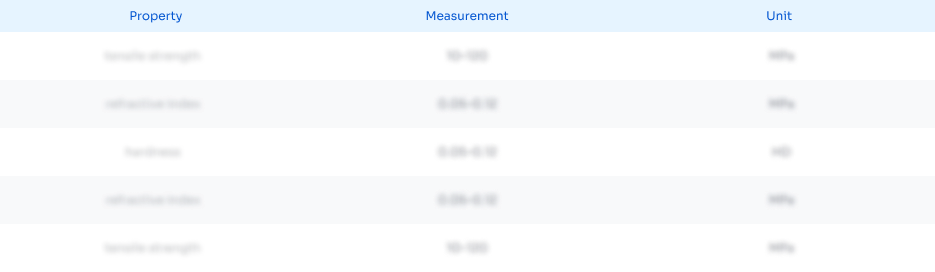
Abstract
Description
Claims
Application Information

- R&D
- Intellectual Property
- Life Sciences
- Materials
- Tech Scout
- Unparalleled Data Quality
- Higher Quality Content
- 60% Fewer Hallucinations
Browse by: Latest US Patents, China's latest patents, Technical Efficacy Thesaurus, Application Domain, Technology Topic, Popular Technical Reports.
© 2025 PatSnap. All rights reserved.Legal|Privacy policy|Modern Slavery Act Transparency Statement|Sitemap|About US| Contact US: help@patsnap.com