The general assembly structure of the coiled tube body of the coiled tube heat exchanger and its winding assembly method
A technology of coiled-tube heat exchangers and heat exchange tubes, applied in indirect heat exchangers, heat exchanger types, heat exchanger shells, etc. Leakage and other problems, to achieve the effect of preventing fluid vibration and collision wear, improving reliability and safety, and enhancing connection strength
- Summary
- Abstract
- Description
- Claims
- Application Information
AI Technical Summary
Problems solved by technology
Method used
Image
Examples
Embodiment Construction
[0039] The present invention will be described in further detail below in conjunction with the accompanying drawings.
[0040] Such as Figure 1 to Figure 9 The overall assembly structure of a coiled tube heat exchanger is shown, which includes an upper connecting tube 2, an upper cone body 4, a central cylinder body 9, and a lower cone body 10 welded together from top to bottom. And the lower connecting pipe 11, the top of the upper connecting pipe 2 is provided with an upper tube plate 1, the bottom of the lower connecting pipe 11 is provided with a lower tube plate 12, and the outer wall of the central cylinder 9 is surrounded by several layers of spiral heat exchange tubes. 7, the rotation direction of the adjacent two layers of heat exchange tubes 7 is opposite. The middle part is provided with the positioning groove 13 that runs through up and down along the vertical direction, and the two ends of several layers of support bars 6 are stacked successively and then instal...
PUM
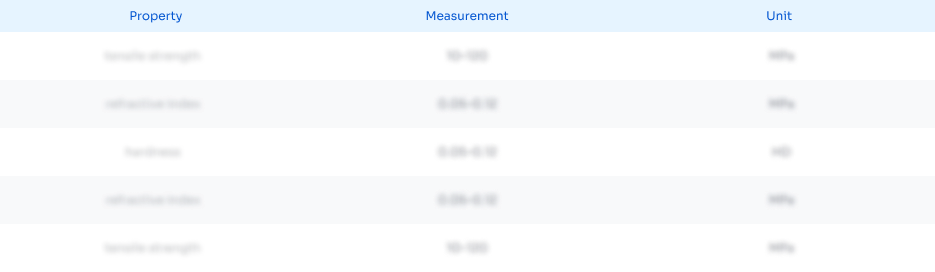
Abstract
Description
Claims
Application Information

- R&D Engineer
- R&D Manager
- IP Professional
- Industry Leading Data Capabilities
- Powerful AI technology
- Patent DNA Extraction
Browse by: Latest US Patents, China's latest patents, Technical Efficacy Thesaurus, Application Domain, Technology Topic, Popular Technical Reports.
© 2024 PatSnap. All rights reserved.Legal|Privacy policy|Modern Slavery Act Transparency Statement|Sitemap|About US| Contact US: help@patsnap.com