High-temperature-resistant unsaturated fatty acid fat microcapsule powder and preparation method thereof
A technology of unsaturated fatty acid and high temperature resistance, which is applied in the direction of oil-containing food ingredients, food preservation, food ingredients as antioxidants, etc. It can solve the problems of short storage period and easy oxidation of unsaturated fatty acid microcapsule powder, and achieve a longer shelf life. And stability, anti-oxidation, good heat resistance
- Summary
- Abstract
- Description
- Claims
- Application Information
AI Technical Summary
Problems solved by technology
Method used
Image
Examples
Embodiment 1
[0037] 1. Preparation of water phase
[0038] Add 41.26g of maltose oligosaccharides, 5g of sodium caseinate, 0.03g of rosemary, 0.03g of tea polyphenols and 1.5g of dipotassium hydrogen phosphate into 150g of water, heat and stir at 60°C to dissolve, and the obtained solid content is 24.2% aqueous phase.
[0039] 2. Preparation of oil phase
[0040] Add 2g of mono- and distearic acid glycerides, 0.05g of natural vitamin E, and 0.03g of tea polyphenols into 50g of cold-pressed linseed oil, heat and dissolve at 60°C to obtain an oil phase.
[0041] 3. Preparation of primary emulsion
[0042] Slowly add the oil phase to the water phase, stir for 2 minutes to fully mix, shear the mixed emulsion at a speed of 20×1000 rpm for 2 minutes, and continuously homogenize the sheared emulsion in a high-pressure homogenizer for 4 Second, the primary pressure is 50bar, and the secondary pressure is 450bar to make primary emulsion.
[0043] 4. Second layer embedding
[0044] Add 0.1g of ...
Embodiment 2
[0050] 1. Preparation of water phase
[0051] 35.2g of maltodextrin, 6g of sodium caseinate, 0.03g of rosemary, 0.02g of phytic acid and 1.6g of dipotassium hydrogen phosphate were added to 150g of water, heated and stirred at 60°C to dissolve, and a solid content of 22.2% was obtained. water box.
[0052] 2. Preparation of oil phase
[0053]Add 2g of glyceryl mono- and distearate and 0.05g of natural vitamin E into 55g of sunflower oil, heat and dissolve at 60°C to obtain an oil phase.
[0054] 3. Preparation of primary emulsion
[0055] Slowly add the oil phase into the water phase, stir for 2 minutes to fully mix, and then shear at a high speed of 20×1000rmp / min for 2 minutes. The sheared emulsion is continuously homogenized in a high-pressure homogenizer for 4 times, the first stage pressure is 50bar, and the second stage is The grade pressure is 450bar, and the primary emulsion is made.
[0056] 4. Second layer embedding
[0057] Add 0.1g of pullulan to 35.7g of wate...
Embodiment 3
[0063] 1. Preparation of water phase
[0064] Add 31.1 g of maltose oligosaccharides, 5 g of sodium caseinate, 0.03 g of rosemary and 1.5 g of dipotassium hydrogen phosphate into 150 g of water, heat and stir at 60° C. to dissolve, and obtain an aqueous phase with a solid content of 20.06%.
[0065] 2. Preparation of oil phase
[0066] Add 2g of glyceryl mono and distearate, 0.05g of natural vitamin E, and 0.02g of ascorbyl palmitate into 60g of camellia oil, heat and dissolve at 60°C to obtain an oil phase.
[0067] 3. Preparation of primary emulsion
[0068] Slowly add the oil phase into the water phase, stir for 2 minutes to fully mix, and then shear at a high speed of 20×1000rmp / min for 2 minutes. The sheared emulsion is continuously homogenized in a high-pressure homogenizer for 4 times, the first stage pressure is 50bar, and the second stage is The grade pressure is 450bar, and the primary emulsion is made.
[0069] 4. Second layer embedding
[0070] Add 0.3g of xant...
PUM
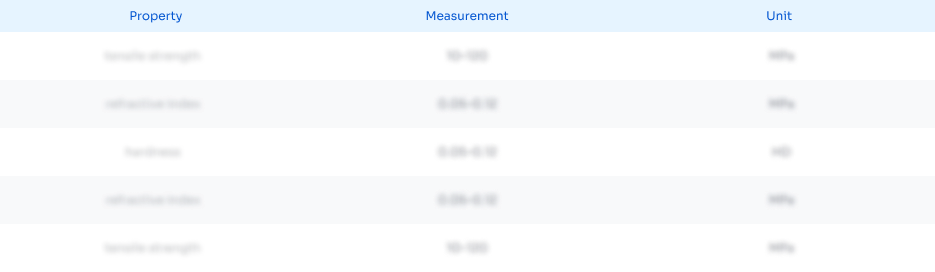
Abstract
Description
Claims
Application Information

- R&D
- Intellectual Property
- Life Sciences
- Materials
- Tech Scout
- Unparalleled Data Quality
- Higher Quality Content
- 60% Fewer Hallucinations
Browse by: Latest US Patents, China's latest patents, Technical Efficacy Thesaurus, Application Domain, Technology Topic, Popular Technical Reports.
© 2025 PatSnap. All rights reserved.Legal|Privacy policy|Modern Slavery Act Transparency Statement|Sitemap|About US| Contact US: help@patsnap.com