Preparation method of heat conducting glue with low viscosity and high thermal conductivity
A high thermal conductivity, thermally conductive adhesive technology, applied in the direction of adhesives, non-polymer adhesive additives, adhesive additives, etc., can solve the problems of high thermally conductive adhesives, difficulty in laminating heavy work, etc., and achieve the effect of good repeatability
- Summary
- Abstract
- Description
- Claims
- Application Information
AI Technical Summary
Problems solved by technology
Method used
Image
Examples
Embodiment 1
[0022] A method for preparing a thermally conductive adhesive with low viscosity and high thermal conductivity, the mass percentage of each component is:
[0023]
[0024] (1) According to the above formula, weigh the dispersant and silane coupling agent and dilute with dimethyl carbonate, add thermal conductive fillers BN and Al 2 0 3 , use a homogenizer at a speed of 1500rpm, mix for 2min;
[0025] (2) Add pressure-sensitive adhesive, and use a homogenizer to mix for 2 minutes at a speed of 1500 rpm;
[0026] (3) Add leveling agent, defoamer and wetting agent, and mix for 1 min at a speed of 1500 rpm using a homogenizer;
[0027] (4) Add epoxy curing agent, and use a homogenizer to mix for 1 min at a speed of 1500 rpm;
[0028] (5) Coating the mixture on both sides of the substrate, curing and drying at 80-90° C. for 10-20 minutes, to obtain a thermally conductive adhesive with low viscosity and high thermal conductivity.
Embodiment 2
[0030] A method for preparing a thermally conductive adhesive with low viscosity and high thermal conductivity, the mass percentage of each component is:
[0031]
[0032] (1) According to the above formula, weigh the dispersant, titanate and silane coupling agent and dilute with ethyl acetate, add the thermal conductive filler Al(OH) 3 and Al 2 0 3 , use a homogenizer at a speed of 1500rpm, mix for 2min;
[0033] (2) Add pressure-sensitive adhesive, and use a homogenizer to mix for 2 minutes at a speed of 1500 rpm;
[0034] (3) Add leveling agent, defoamer and wetting agent, and mix for 1 min at a speed of 1500 rpm using a homogenizer;
[0035] (4) Add epoxy curing agent, and use a homogenizer to mix for 1 min at a speed of 1500 rpm;
[0036] (5) Coating the mixture on both sides of the substrate, curing and drying at 80-90° C. for 10-20 minutes, to obtain a thermally conductive adhesive with low viscosity and high thermal conductivity.
PUM
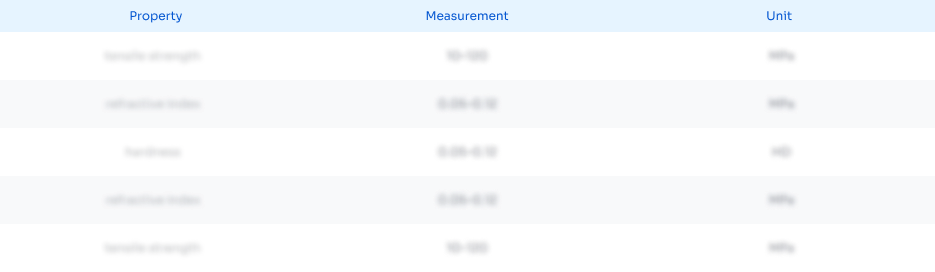
Abstract
Description
Claims
Application Information

- R&D
- Intellectual Property
- Life Sciences
- Materials
- Tech Scout
- Unparalleled Data Quality
- Higher Quality Content
- 60% Fewer Hallucinations
Browse by: Latest US Patents, China's latest patents, Technical Efficacy Thesaurus, Application Domain, Technology Topic, Popular Technical Reports.
© 2025 PatSnap. All rights reserved.Legal|Privacy policy|Modern Slavery Act Transparency Statement|Sitemap|About US| Contact US: help@patsnap.com