A kind of preparation method of shape memory alloy with exchange bias effect
A technology of memory alloy and bias effect, which is applied in the field of preparation of shape memory alloy with exchange bias effect, can solve the problems of low temperature and unfavorable practical application of materials, and achieve the effect of low preparation cost, low cost and simple process
- Summary
- Abstract
- Description
- Claims
- Application Information
AI Technical Summary
Problems solved by technology
Method used
Image
Examples
Embodiment 1
[0023] Example 1: Mn 2 Preparation process of NiAl ribbon sample
[0024] Step 1: Follow Mn 2 Calculate the mass of each element required by the NiAl chemical formula, and use an electronic balance to weigh the metal element Mn: 5.8356g (0.106mol), Ni: 2.9999g (0.053mol) and Al: 1.3789g (0.053mol) with a purity of 99.99%; Prepare a piece of unoxidized metal zirconium ingot;
[0025] The second step: Put the unoxidized metal zirconium ingot and the weighed metal element into the electric arc furnace. Use mechanical pump and molecular pump to pump the vacuum in the electric arc furnace to 2x10 -3 Pa. Then fill with argon to atmospheric pressure;
[0026] Step 3: Use an electric arc with a current of 50A to melt the metal zirconium ingot to ensure that the alloy will not be oxidized during the melting process. After the arc is stable, use an electric arc with a current of 85A to melt the prepared metal element. Prepare a uniform ingot-like sample after repeated smelting for...
Embodiment 2
[0030] Example 2: Mn 1.9 co 0.1 Preparation process of NiAl ribbon sample
[0031] Step 1: Follow Mn 1.9 co 0.1 Calculate the mass of each element required by the NiAl chemical formula, and use an electronic balance to weigh Mn: 3.9016g (0.071mol), Ni: 2.0952g (0.037mol), Al: 0.9628g (0.037mol) and Co : 0.2104g (0.004mol); Prepare a piece of unoxidized metal zirconium ingot;
[0032] The second step: Put the unoxidized metal zirconium ingot and the weighed metal element into the electric arc furnace. Use mechanical pump and molecular pump to pump the vacuum in the electric arc furnace to 2x10 -3 Pa and then filled with argon to atmospheric pressure;
[0033]Step 3: Use an electric arc with a current of 50A to melt the metal zirconium ingot to ensure that the alloy will not be oxidized during the melting process. After the arc is stable, use an electric arc with a current of 85A to melt the prepared metal element. Prepare a uniform ingot-like sample after repeated smelti...
Embodiment 3
[0037] Example 3: Mn 1.8 co 0.2 Preparation process of NiAl ribbon sample
[0038] Step 1: Follow Mn 1.8 co 0.2 Calculate the mass of each metal element required by the NiAl chemical formula, and weigh the metal element Mn with a purity of 99.99%: 3.6994g (0.067mol), Ni: 2.0957g (0.037mol), Al: 0.9627g (0.037mol) and Co : 0.4207g (0.007mol); prepare a piece of unoxidized metal zirconium ingot;
[0039] The second step: Put the unoxidized metal zirconium ingot and the weighed metal element into the electric arc furnace. Use mechanical pump and molecular pump to pump the vacuum in the electric arc furnace to 2x10 -3 Pa and then filled with argon to atmospheric pressure;
[0040] Step 3: Use an electric arc with a current of 50A to melt the metal zirconium ingot to ensure that the alloy will not be oxidized during the melting process. After the arc is stable, use an electric arc with a current of 85A to melt the prepared metal element. Prepare a uniform ingot-like sample a...
PUM
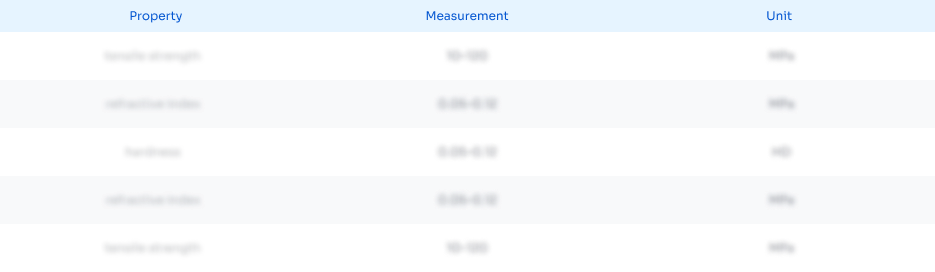
Abstract
Description
Claims
Application Information

- R&D Engineer
- R&D Manager
- IP Professional
- Industry Leading Data Capabilities
- Powerful AI technology
- Patent DNA Extraction
Browse by: Latest US Patents, China's latest patents, Technical Efficacy Thesaurus, Application Domain, Technology Topic, Popular Technical Reports.
© 2024 PatSnap. All rights reserved.Legal|Privacy policy|Modern Slavery Act Transparency Statement|Sitemap|About US| Contact US: help@patsnap.com