Assembling and welding process method for stator machine seat
A technology of assembly welding and process method, applied in the field of assembly welding process of air-cooled air-conditioning camera stator frame, can solve the problems of large influence of overall structure and size, long operation cycle, difficult operation, etc. The effect of improving assembly accuracy
- Summary
- Abstract
- Description
- Claims
- Application Information
AI Technical Summary
Problems solved by technology
Method used
Image
Examples
Embodiment Construction
[0010] A stator frame assembly welding process method, (1) material preparation: perform blanking, sand blasting, molding, and processing on all parts of the frame according to the requirements of the drawing; (2) separate assembly and welding: separate the bottom side plate and the connecting strip Form the frame plate and flatten it after welding; divide the skeleton of the machine base into five parts and assemble them vertically, and reconfirm the cross centerline after welding; (3) skeleton assembly: as figure 1 , put the bottom frame plate 1 flat on the platform, adjust the unevenness and fix it by lap welding, use the pier to support the big bottom corner and place it on both sides of the frame plate for temporary lap welding and fixation, and put the 5 groups of skeletons that have completed sub-assembly welding on the frame On the board, adjust the total length of the machine base and the distance between each group, adjust the concentricity of the inner circle in comb...
PUM
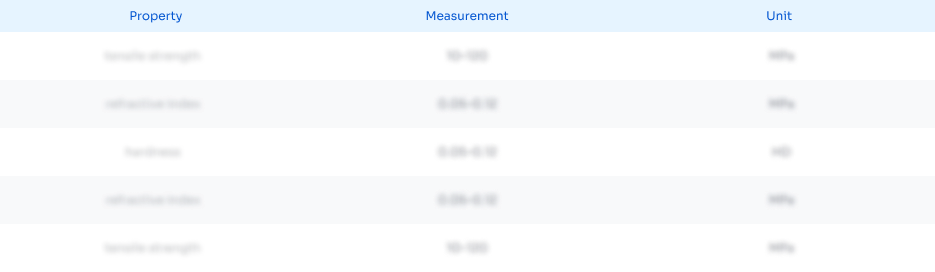
Abstract
Description
Claims
Application Information

- R&D
- Intellectual Property
- Life Sciences
- Materials
- Tech Scout
- Unparalleled Data Quality
- Higher Quality Content
- 60% Fewer Hallucinations
Browse by: Latest US Patents, China's latest patents, Technical Efficacy Thesaurus, Application Domain, Technology Topic, Popular Technical Reports.
© 2025 PatSnap. All rights reserved.Legal|Privacy policy|Modern Slavery Act Transparency Statement|Sitemap|About US| Contact US: help@patsnap.com