Preparation method of ZnO-ZrO2@Al2O3@SAPO-34 dual-core-shell catalyst
A core-shell catalyst, 2·6H2O technology, applied in the chemical industry, can solve the problems of poor catalytic effect of composite catalysts, poor anti-sintering stability, etc., and achieve the effects of inhibiting the formation of by-products, alleviating the formation of carbon deposits, and enhancing selectivity.
- Summary
- Abstract
- Description
- Claims
- Application Information
AI Technical Summary
Problems solved by technology
Method used
Examples
Embodiment 1
[0011] A ZnO-ZrO 2 @Al 2 o 3 The preparation method of @SAPO-34 double core-shell catalyst comprises the following steps:
[0012] (1) ZnO-ZrO 2 @Al 2 o 3 Preparation: According to the molar ratio of raw materials NH 4 CO 3 :Zr(NO 3 ) 4 ·5H 2 O: Zn(NO 3 ) 2 ·6H 2 O=2.2:1.0:0.2, under stirring, flow 1.0mol L at a flow rate of 3ml / min -1 Add the ammonium carbonate solution to the zinc-zirconium mixed solution to form a precipitate, keep stirring and aging at 70°C for 2h, cool to room temperature, filter, wash, dry at 110°C for 4h, and roast at 500°C for 3h to obtain ZnO-ZrO 2 Powder; according to the core-shell mass ratio Al 2 o 3 :ZnO-ZrO 2 =1:2 Al 2 o 3 Spray on ZnO-ZrO 2 On the surface, dry at 105°C for 1h and bake at 600°C for 3h to obtain ZnO-ZrO 2 @Al 2 o 3 powder.
[0013] (2) ZnO-ZrO 2 @Al 2 o 3 Preparation of @SAPO-34 double-core-shell catalyst: according to the molar ratio of raw materials Al 2 o 3 :P 2 o 5 :SiO2 2 :MOR:H 2 O=1.0:0.8:0.6...
Embodiment 2
[0016] A ZnO-ZrO 2 @Al 2 o 3 The preparation method of @SAPO-34 double core-shell catalyst comprises the following steps:
[0017] (1) ZnO-ZrO 2 @Al2 o 3 Preparation: According to the molar ratio of raw materials NH 4 CO 3 :Zr(NO 3 ) 4 ·5H 2 O: Zn(NO 3 ) 2 ·6H 2 O=2.2:1.0:0.2, under stirring, flow 1.0mol L at a flow rate of 3ml / min -1 Add the ammonium carbonate solution to the zinc-zirconium mixed solution to form a precipitate, keep stirring and aging at 70°C for 2h, cool to room temperature, filter, wash, dry at 110°C for 4h, and roast at 500°C for 3h to obtain ZnO-ZrO 2 Powder; according to the core-shell mass ratio Al 2 o 3 :ZnO-ZrO 2 =1:4 Al 2 o 3 Spray on ZnO-ZrO 2 On the surface, dry at 105°C for 1h and bake at 600°C for 3h to obtain ZnO-ZrO 2 @Al 2 o 3 powder.
[0018] (2) ZnO-ZrO 2 @Al 2 o 3 Preparation of @SAPO-34 double-core-shell catalyst: according to the molar ratio of raw materials Al 2 o 3 :P 2 o 5 :SiO2 2 :MOR:H 2 O =1.0:0.8:0.6:...
Embodiment 3
[0021] A ZnO-ZrO 2 @Al 2 o 3 The preparation method of @SAPO-34 double core-shell catalyst comprises the following steps:
[0022] (1) ZnO-ZrO 2 @Al 2 o 3 Preparation: According to the molar ratio of raw materials NH 4 CO 3 :Zr(NO 3 ) 4 ·5H 2 O: Zn(NO 3 ) 2 ·6H 2 O=2.2:1.0:0.2, under stirring, flow 1.0mol L at a flow rate of 3ml / min -1 Add the ammonium carbonate solution to the zinc-zirconium mixed solution to form a precipitate, keep stirring and aging at 70°C for 2h, cool to room temperature, filter, wash, dry at 110°C for 4h, and roast at 500°C for 3h to obtain ZnO-ZrO 2 Powder; according to the core-shell mass ratio Al 2 o 3 :ZnO-ZrO 2 =1:6 Al 2 o 3 Spray on ZnO-ZrO 2 On the surface, dry at 105°C for 1h and bake at 600°C for 3h to obtain ZnO-ZrO 2 @Al 2 o 3 powder.
[0023] (2) ZnO-ZrO 2 @Al 2 o 3 Preparation of @SAPO-34 double-core-shell catalyst: according to the molar ratio of raw materials Al 2 o 3 :P 2 o 5 :SiO2 2 :MOR:H 2 O =1.0:0.8:0....
PUM
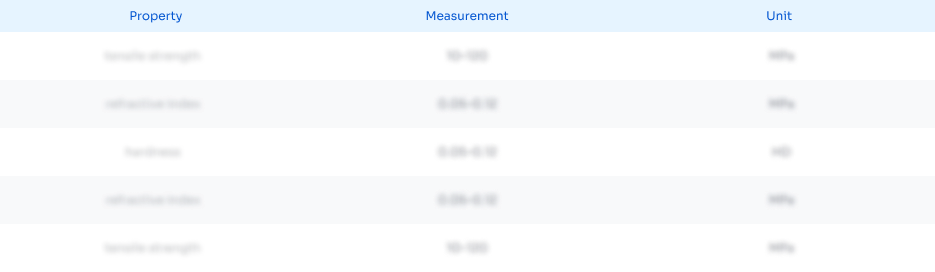
Abstract
Description
Claims
Application Information

- R&D
- Intellectual Property
- Life Sciences
- Materials
- Tech Scout
- Unparalleled Data Quality
- Higher Quality Content
- 60% Fewer Hallucinations
Browse by: Latest US Patents, China's latest patents, Technical Efficacy Thesaurus, Application Domain, Technology Topic, Popular Technical Reports.
© 2025 PatSnap. All rights reserved.Legal|Privacy policy|Modern Slavery Act Transparency Statement|Sitemap|About US| Contact US: help@patsnap.com