Mechanical pump set assembling method for molten steel degassing and mechanical pump set system
A composition method and mechanical pump technology, applied in the direction of elastic fluid rotary piston type/oscillating piston type pump combination, mechanical equipment, machine/engine, etc., can solve the loss of pumping capacity and gas load distribution of a pump group module Inhomogeneity, lack of adjustment performance and other problems, to achieve the effect of low long-term operation and maintenance costs, good adjustable performance, and wide adjustment range
- Summary
- Abstract
- Description
- Claims
- Application Information
AI Technical Summary
Problems solved by technology
Method used
Image
Examples
Embodiment 1
[0057] A method for composing a mechanical pump unit for molten steel degassing. It is composed of a plurality of pumps A. Each pump unit is connected in parallel with the intake manifold and then connected to the suction port of the vacuum tank, and the exhaust port of each pump unit is connected with The outlet header is connected in parallel and connected to the atmosphere;
[0058] The suction port of the vacuum tank is connected with the suction port of the molten steel degassing device that needs to be evacuated;
[0059] Each pump group includes at least a first-stage pump, a second-stage pump, and a third-stage pump (the first-stage pump, the second-stage pump, the third-stage pump, the fourth-stage pump, and the fifth-stage pump in this case are the first-stage pump unit and the second-stage pump respectively. Unit, three-stage pump unit, four-stage pump unit, and five-stage pump unit), and the first-stage pump, second-stage pump, and third-stage pump adopt large air volum...
Embodiment 2
[0076] See Figure 1-Figure 3 , The structure shown is the three mechanical pump system designed based on the above method, among which:
[0077] figure 1 Shown in is the first type of mechanical pump system. Multiple pump groups A are connected in parallel with the intake manifold 610 through pipes and then connected to the vacuum tank 500. Each pump group is composed of a five-stage pump group unit. The group unit is formed by connecting at least two pumps in parallel, and the exhaust port of each pump group is connected in parallel with the gas outlet header;
[0078] Further, the five-level pump unit units are:
[0079] The first-stage pump unit (first-stage pump) 100 is composed of 5 Roots vacuum pumps with an effective suction capacity of 25000 m3 / h@67Pa 20℃ in parallel;
[0080] The two-stage pump unit (two-stage pump) 200 is composed of 3 18000~20000 m3 / h Roots vacuum pumps in parallel;
[0081] The three-stage pump unit (three-stage pump) 300 is composed of two 4000~10000 m3 / ...
Embodiment 3
[0094] See figure 2 , The second type of mechanical pump system is shown. The difference from the second embodiment is:
[0095] The exhaust port of the four-stage pump unit is connected in parallel with the exhaust branch pipe 630, and the exhaust branch pipe 630 is connected in parallel with the exhaust port of the five-stage pump unit through the intake branch pipe 640. This method can increase the stability and adjustability of the entire mechanical pumping system.
PUM
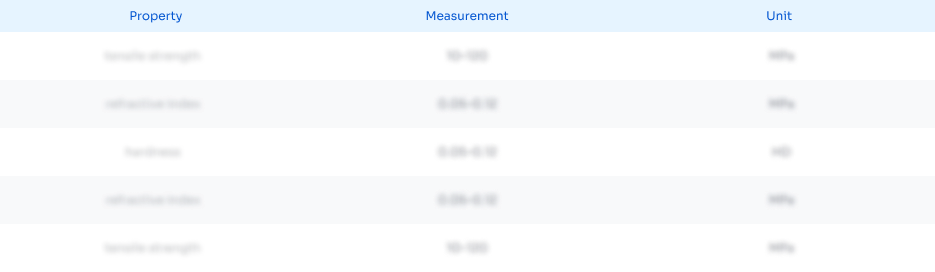
Abstract
Description
Claims
Application Information

- R&D
- Intellectual Property
- Life Sciences
- Materials
- Tech Scout
- Unparalleled Data Quality
- Higher Quality Content
- 60% Fewer Hallucinations
Browse by: Latest US Patents, China's latest patents, Technical Efficacy Thesaurus, Application Domain, Technology Topic, Popular Technical Reports.
© 2025 PatSnap. All rights reserved.Legal|Privacy policy|Modern Slavery Act Transparency Statement|Sitemap|About US| Contact US: help@patsnap.com