Microbubble injection moulding ABS composite material and preparation method thereof
A composite material and micro-foaming technology, applied in the field of polymer materials, can solve the problems of reduced mechanical properties of ABS, collapse and rupture of gas bubbles, low melt strength, etc., to improve tensile strength, improve fluidity, and improve melt the effect of strength
- Summary
- Abstract
- Description
- Claims
- Application Information
AI Technical Summary
Problems solved by technology
Method used
Image
Examples
Embodiment 1
[0033] The present embodiment provides a kind of preparation method of microfoaming injection molding ABS composite material, comprises the following steps:
[0034] Put 64.85 parts of ABS, 10 parts of heat-resistant agent, 5 parts of toughening agent, 0.05 part of crosslinking agent and 0.1 part of antioxidant into a high-speed mixer according to the stated weight ratio and mix for 4-6 minutes to obtain a homogeneous mixture of the above components . Put the above-mentioned component mixture into the twin-screw extruder from the hopper, add 20 parts of SAN resin to the second half of the screw to extrude and granulate, and obtain high-fluidity and high-melt strength ABS composite materials; the temperature of each section of the extruder As follows: Zone 1 200~220℃, Zone 2 200~225℃, Zone 3 210~220℃, Zone 4 200~225℃, Zone 5 210~225℃, Zone 6 215~230℃, Zone 7 215~230℃ , head temperature 220 ~ 230 ℃, pressure 12 ~ 18MPa, the material stays in the extruder for 1 ~ 2min.
[0035]...
Embodiment 2
[0038] 64.85 parts of ABS, 10 parts of heat-resistant agent, 5 parts of toughening agent, 0.1 part of crosslinking agent and 0.1 part of antioxidant are put into a high-speed mixer according to the weight ratio and mixed for 4-6 minutes to obtain a uniform mixture of the above components. Put the above component mixture into the twin-screw extruder from the hopper, add 20 parts of SAN resin to the second half of the screw to extrude and granulate, and obtain high fluidity and high melt strength ABS composite material; the temperature of each section of the extruder As follows: Zone 1 200~220℃, Zone 2 200~225℃, Zone 3 210~220℃, Zone 4 200~225℃, Zone 5 210~225℃, Zone 6 215~230℃, Zone 7 215~230℃ , head temperature 220 ~ 230 ℃, pressure 12 ~ 18MPa, the material stays in the extruder for 1 ~ 2min.
[0039] Put 98 parts of high fluidity and high melt strength ABS composite material and 2 parts of modified sodium bicarbonate foaming agent masterbatch into a mixer and mix to obtain a ...
Embodiment 3
[0042] 64.85 parts of ABS, 10 parts of heat-resistant agent, 5 parts of toughening agent, 0.5 part of crosslinking agent and 0.1 part of antioxidant are put into a high-speed mixer according to the weight ratio and mixed for 4-6 minutes to obtain a uniform mixture of the above components. Put the above component mixture into the twin-screw extruder from the hopper, add 20 parts of SAN resin to the second half of the screw to extrude and granulate, and obtain high fluidity and high melt strength ABS composite material; the temperature of each section of the extruder As follows: Zone 1 200~220℃, Zone 2 200~225℃, Zone 3 210~220℃, Zone 4 200~225℃, Zone 5 210~225℃, Zone 6 215~230℃, Zone 7 215~230℃ , head temperature 220 ~ 230 ℃, pressure 12 ~ 18MPa, the material stays in the extruder for 1 ~ 2min.
[0043]Put 98 parts of high fluidity and high melt strength ABS composite material and 2 parts of modified sodium bicarbonate foaming agent masterbatch into a mixer and mix to obtain a m...
PUM
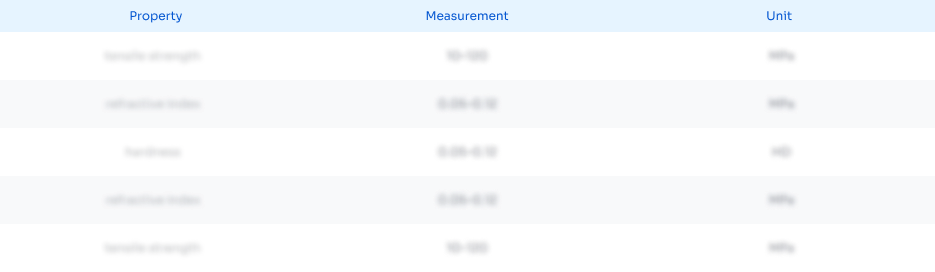
Abstract
Description
Claims
Application Information

- R&D Engineer
- R&D Manager
- IP Professional
- Industry Leading Data Capabilities
- Powerful AI technology
- Patent DNA Extraction
Browse by: Latest US Patents, China's latest patents, Technical Efficacy Thesaurus, Application Domain, Technology Topic, Popular Technical Reports.
© 2024 PatSnap. All rights reserved.Legal|Privacy policy|Modern Slavery Act Transparency Statement|Sitemap|About US| Contact US: help@patsnap.com