Application method of circulating fluidized bed roasting rotary integrated furnace
A circulating fluidized bed and integrated technology, which is applied in the fields of environmental protection and resource recycling comprehensive utilization, can solve problems such as the inability to meet the temperature conditions of the roasting activation process, and achieve the effects of reducing production costs and environmental pollution
- Summary
- Abstract
- Description
- Claims
- Application Information
AI Technical Summary
Problems solved by technology
Method used
Image
Examples
Embodiment Construction
[0034] The present invention will be further described below in conjunction with the accompanying drawings and specific embodiments.
[0035] Such as figure 1 , figure 2 , image 3 , Figure 4 , Figure 5 , Figure 6 As shown, a method for using a circulating fluidized bed roasting rotary integrated furnace is characterized in that:
[0036] Step 1, the coal is fluidized and burned in the hearth 24 of the circulating fluidized bed coal-fired furnace II and then enters the cyclone separator 23, and the larger high-temperature solid particles separated by the cyclone separator 23 enter the return system 25, and the high-temperature solid particles A material column is formed in the standpipe 28 of the feeder 26. There is a U-shaped valve 29 between the standpipe 28 and the return pipe 30. There is an equal pressure air chamber at the bottom of the U-shaped valve 29 to supply air to ensure the fluidization of high-temperature solid particles. The standpipe The pressure dif...
PUM
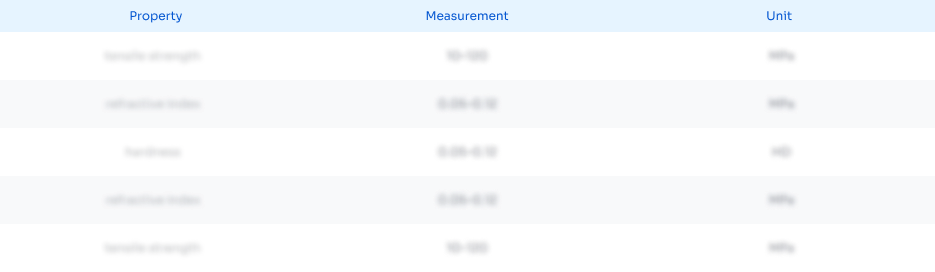
Abstract
Description
Claims
Application Information

- R&D
- Intellectual Property
- Life Sciences
- Materials
- Tech Scout
- Unparalleled Data Quality
- Higher Quality Content
- 60% Fewer Hallucinations
Browse by: Latest US Patents, China's latest patents, Technical Efficacy Thesaurus, Application Domain, Technology Topic, Popular Technical Reports.
© 2025 PatSnap. All rights reserved.Legal|Privacy policy|Modern Slavery Act Transparency Statement|Sitemap|About US| Contact US: help@patsnap.com