Preparation process of waterproof flame-retardant polyamide fiber fabric
A technology of flame-retardant polyamide and fiber fabrics, which is applied in the field of textile manufacturing, can solve the problems of not being able to find the dyeing effect of synthetic fiber fabrics, and achieve the effects of increasing adhesion stability, significant effects, and improving uniformity
- Summary
- Abstract
- Description
- Claims
- Application Information
AI Technical Summary
Problems solved by technology
Method used
Image
Examples
Embodiment 1
[0027] The preparation process of the waterproof and flame-retardant polyamide fiber fabric includes: pre-treatment process and printing, waterproof and flame-retardant layer coating process.
[0028] Among them, the parameters in each step are set as follows:
[0029] During cold pad-batch treatment, use 40g / L caustic soda and 8g / L hydrogen peroxide to pad the gray cloth. After padding, roll and stack it for 12 hours. The gray cloth is a thick sparse fabric above 1000D.
[0030] When scouring, first carry out immersion, and then carry out steaming. Among them, the immersion method is five immersion and five rolling, the liquid carrying rate is 80%, and the tension of the washing machine is set to 4Mpa; the auxiliaries of the immersion liquid include desizing and refining agent YZ-1118, chelating agent, caustic soda, hydrogen peroxide, and water glass. The concentration of desizing and scouring agent is 4g / L, the concentration of chelating agent is 2g / L, the concentration of ...
Embodiment 2
[0046] The difference between this embodiment and embodiment 1 is that only caustic soda is used during the cold pad batch in the present embodiment;
[0047]The immersion method during scouring is five immersion and five rolling, and the additives for immersion are desizing and scouring agent YZ-1118, caustic soda, hydrogen peroxide, wherein the concentration of desizing and scouring agent is 5g / L, and the concentration of caustic soda is 20g / L. The concentration of hydrogen peroxide is 12g / L; the speed of steaming is 50m / min, the time is 60min, and the temperature is 70°C; the liquid carrying rate after padding is 60%; the tension of the washing machine is 4MPa;
[0048] When setting the shape, the vehicle speed is 80m / min, and the temperature is 220°C.
Embodiment 3
[0050] The difference between this embodiment and Embodiment 1 lies in that the concentrations of caustic soda and hydrogen peroxide used during cold pad batching in this embodiment are different, the contents of additives in the immersion solution are different, and the temperature and vehicle speed are different during shaping. The specific settings are as follows:
[0051] Adopt concentration during described cold pad batch to be that the caustic soda of 35g / L and the hydrogen peroxide of 9g / L carry out padding to gray cloth;
[0052] During scouring, five immersion and five rolling methods are used to immerse the liquid, and then steam; the auxiliary agents for the immersion liquid include desizing and scouring agent, chelating agent, caustic soda, hydrogen peroxide, and water glass, wherein the concentration of the desizing and scouring agent is 3g / L, the concentration of chelating agent is 3g / L, and the concentration of caustic soda is 8g / L, and the concentration of hyd...
PUM
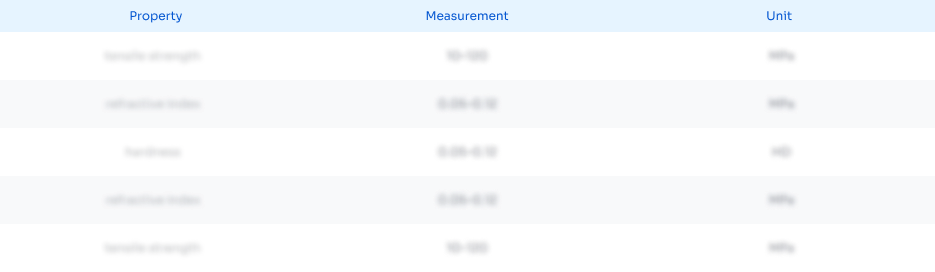
Abstract
Description
Claims
Application Information

- R&D
- Intellectual Property
- Life Sciences
- Materials
- Tech Scout
- Unparalleled Data Quality
- Higher Quality Content
- 60% Fewer Hallucinations
Browse by: Latest US Patents, China's latest patents, Technical Efficacy Thesaurus, Application Domain, Technology Topic, Popular Technical Reports.
© 2025 PatSnap. All rights reserved.Legal|Privacy policy|Modern Slavery Act Transparency Statement|Sitemap|About US| Contact US: help@patsnap.com