Value calculating method of thermal residual stress of fiber reinforced composite material under low temperature
A composite material and residual stress technology, which is applied in calculation, image data processing, 3D modeling, etc., can solve the problems of complex cost, difficulty in accurately measuring the microscopic residual stress of composite materials, etc., so as to achieve real and reliable calculation results and better calculation results. Effect
- Summary
- Abstract
- Description
- Claims
- Application Information
AI Technical Summary
Problems solved by technology
Method used
Image
Examples
Embodiment
[0042] The improved fiber random distribution algorithm proposed by the present invention is shown in the schematic diagram figure 2 , See the flowchart image 3 . Specific steps are as follows:
[0043] ①Set the initial parameters, including the length a and width b of the target window, fiber diameter d f , Target fiber volume content Minimum fiber spacing l min And maximum fiber spacing l max .
[0044] ② In the target window with length a and width b, take the center of the window as the origin of coordinates, the horizontal direction as the x-axis, and the vertical direction as the y-axis. In the center area of the window (for example, take |x 1 | 1 | figure 2 The dashed box in a) randomly fill in a point (x 1 ,y 1 ) As the center of the first fiber.
[0045] ③Fill in the second point (x 2 ,y 2 ) As the center of the second fiber, the position of the point is determined by two parameters: point (x 1 ,y 1 ) And point (x 2 ,y 2 ) Distance l 1 , And the direction angle θ b...
PUM
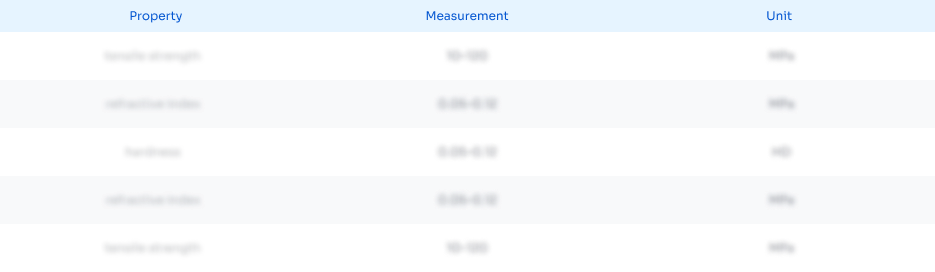
Abstract
Description
Claims
Application Information

- R&D
- Intellectual Property
- Life Sciences
- Materials
- Tech Scout
- Unparalleled Data Quality
- Higher Quality Content
- 60% Fewer Hallucinations
Browse by: Latest US Patents, China's latest patents, Technical Efficacy Thesaurus, Application Domain, Technology Topic, Popular Technical Reports.
© 2025 PatSnap. All rights reserved.Legal|Privacy policy|Modern Slavery Act Transparency Statement|Sitemap|About US| Contact US: help@patsnap.com