A kind of preparation method of preform, fiber fabric intermediate
A technology of fiber fabrics and intermediates, applied in the direction of coating, etc., can solve the problems of RTM resin incompatibility, small fabrics, low production efficiency, etc., to improve regularity and fiber volume content, reduce the number of pressing rolls, and reduce preparation effect of difficulty
- Summary
- Abstract
- Description
- Claims
- Application Information
AI Technical Summary
Problems solved by technology
Method used
Image
Examples
example 1
[0035] RTM resin: 6818 high temperature curing epoxy resin system
[0036] Dry fabric: G0827 unidirectional carbon fiber fabric, surface density 165g / m 2 , fiber type T300-3k.
[0037] Step 1: Use high-temperature curing 6818RTM epoxy resin as the sizing agent material for dry fabrics, and apply 6818RTM epoxy resin to a thickness of 10g / m2±2g / m2 using the glue applicator of the hot-melt method prepreg production equipment resin film;
[0038] Step 2: Place the rolled G0827 unidirectional carbon fiber fabric on the dipping machine of the hot-melt prepreg equipment, and apply the prepared 6818RTM epoxy resin film on the surface of the dry fabric through only one pressure roller, and try to Avoid pressing the resin film into the fiber interior;
[0039] The third step: After the dry fabric is pre-impregnated, the G0827 unidirectional carbon fiber fabric intermediate that is similar to the hot-melt fabric prepreg is obtained with a release paper on one side and a plastic film o...
example 2
[0042] RTM resin: 6818 high temperature curing epoxy resin system
[0043] Dry fabric: G0827 unidirectional carbon fiber fabric, surface density 165g / m 2 , fiber type T300-3k.
[0044] Step 1: Use high-temperature curing 6818RTM epoxy resin as the sizing agent material for dry fabrics, and apply 6818RTM epoxy resin to a thickness of 20g / m2±2g / m2 using the glue applicator of the hot-melt method prepreg production equipment resin film;
[0045] Step 2: Place the rolled G0827 unidirectional carbon fiber fabric on the dipping machine of the hot-melt prepreg equipment, and apply the prepared 6818RTM epoxy resin film on the surface of the dry fabric through only one pressure roller, and try to Avoid pressing the resin film into the fiber interior;
[0046] Step 3: After the dry fabric is pre-impregnated, one side is a release paper and the other side is a plastic film, which is similar to the G0827 unidirectional carbon fiber fabric intermediate of the hot-melt fabric prepreg; th...
PUM
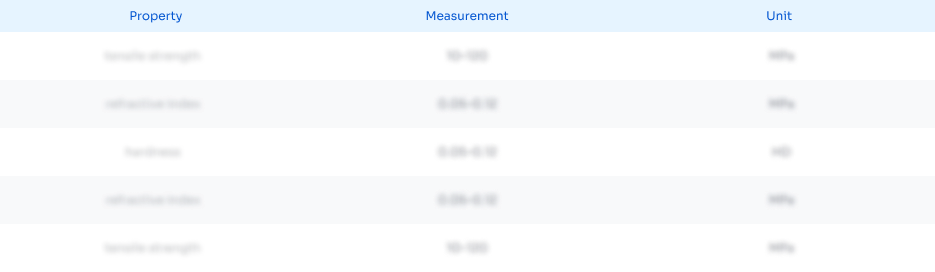
Abstract
Description
Claims
Application Information

- R&D
- Intellectual Property
- Life Sciences
- Materials
- Tech Scout
- Unparalleled Data Quality
- Higher Quality Content
- 60% Fewer Hallucinations
Browse by: Latest US Patents, China's latest patents, Technical Efficacy Thesaurus, Application Domain, Technology Topic, Popular Technical Reports.
© 2025 PatSnap. All rights reserved.Legal|Privacy policy|Modern Slavery Act Transparency Statement|Sitemap|About US| Contact US: help@patsnap.com