Difluoroethanol synthesis process
A technology for difluoroethanol and synthesis process, which is applied in the field of synthesis technology of difluoroethanol, can solve problems such as difficulty in recycling, and achieve the effects of few steps, good process economy and simple process
- Summary
- Abstract
- Description
- Claims
- Application Information
AI Technical Summary
Problems solved by technology
Method used
Examples
Embodiment 1
[0014] Add 860.9g of γ-butyrolactone and 149.6g of potassium hydroxide into the dry reaction kettle, then introduce 201g of 2,2-difluoro-1-chloroethane through the liquid phase port, then rapidly raise the temperature to 180°C, and react for 4h . The resulting reaction solution was filtered, distilled, and then dried through 4A molecular sieves to obtain the difluoroethanol product with a purity of 99.93% and a yield of 92.3%.
[0015] After the reaction solution was filtered, the solid was stirred with 1000 mL of anhydrous methanol at room temperature for 2 h, filtered, and dried to obtain potassium chloride; the filtrate was evaporated to dryness under reduced pressure to obtain potassium acetate. After drying, 94.4 g of potassium hydroxybutyrate was obtained, with a recovery rate of 96.1%.
Embodiment 2
[0017] Add 858.9g of γ-butyrolactone and 130.9g of potassium hydroxide into the dry reaction kettle, then introduce 200g of 2,2-difluoro-1-chloroethane through the liquid phase port, then rapidly raise the temperature to 200°C, and react for 6h . The resulting reaction solution was filtered, distilled, and then dried over anhydrous magnesium sulfate and 4A molecular sieve to obtain the difluoroethanol product with a purity of 99.91% and a yield of 92.7%.
[0018] After the reaction solution was filtered, the solid was stirred with 800 mL of anhydrous methanol at room temperature for 2 h, filtered, and dried to obtain potassium chloride; the filtrate was evaporated to dryness under reduced pressure to obtain potassium acetate. After drying, 48.0 g of potassium hydroxybutyrate was obtained with a recovery rate of 94.5%.
Embodiment 3
[0020] Add 1377.4g of γ-butyrolactone and 137.0g of potassium hydroxide into the dry reaction kettle, and then pass 199g of 2,2-difluoro-1-chloroethane through the liquid phase port, and then rapidly rise to 160°C, and react 8h. The resulting reaction solution was filtered, distilled, and then dried over anhydrous copper sulfate and 4A molecular sieve to obtain the difluoroethanol product with a purity of 99.90% and a yield of 92.1%.
[0021] After the reaction solution was filtered, the solid was stirred with 1000 mL of absolute ethanol at 35°C for 2 hours, filtered, and dried to obtain potassium chloride; the filtrate was evaporated to dryness under reduced pressure to obtain potassium acetate. After drying, 67.0 g of potassium hydroxybutyrate was obtained, with a recovery rate of 97.1%.
PUM
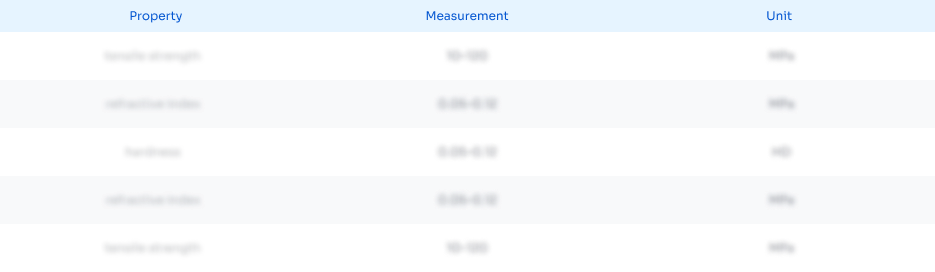
Abstract
Description
Claims
Application Information

- R&D Engineer
- R&D Manager
- IP Professional
- Industry Leading Data Capabilities
- Powerful AI technology
- Patent DNA Extraction
Browse by: Latest US Patents, China's latest patents, Technical Efficacy Thesaurus, Application Domain, Technology Topic, Popular Technical Reports.
© 2024 PatSnap. All rights reserved.Legal|Privacy policy|Modern Slavery Act Transparency Statement|Sitemap|About US| Contact US: help@patsnap.com